Reverse logistics
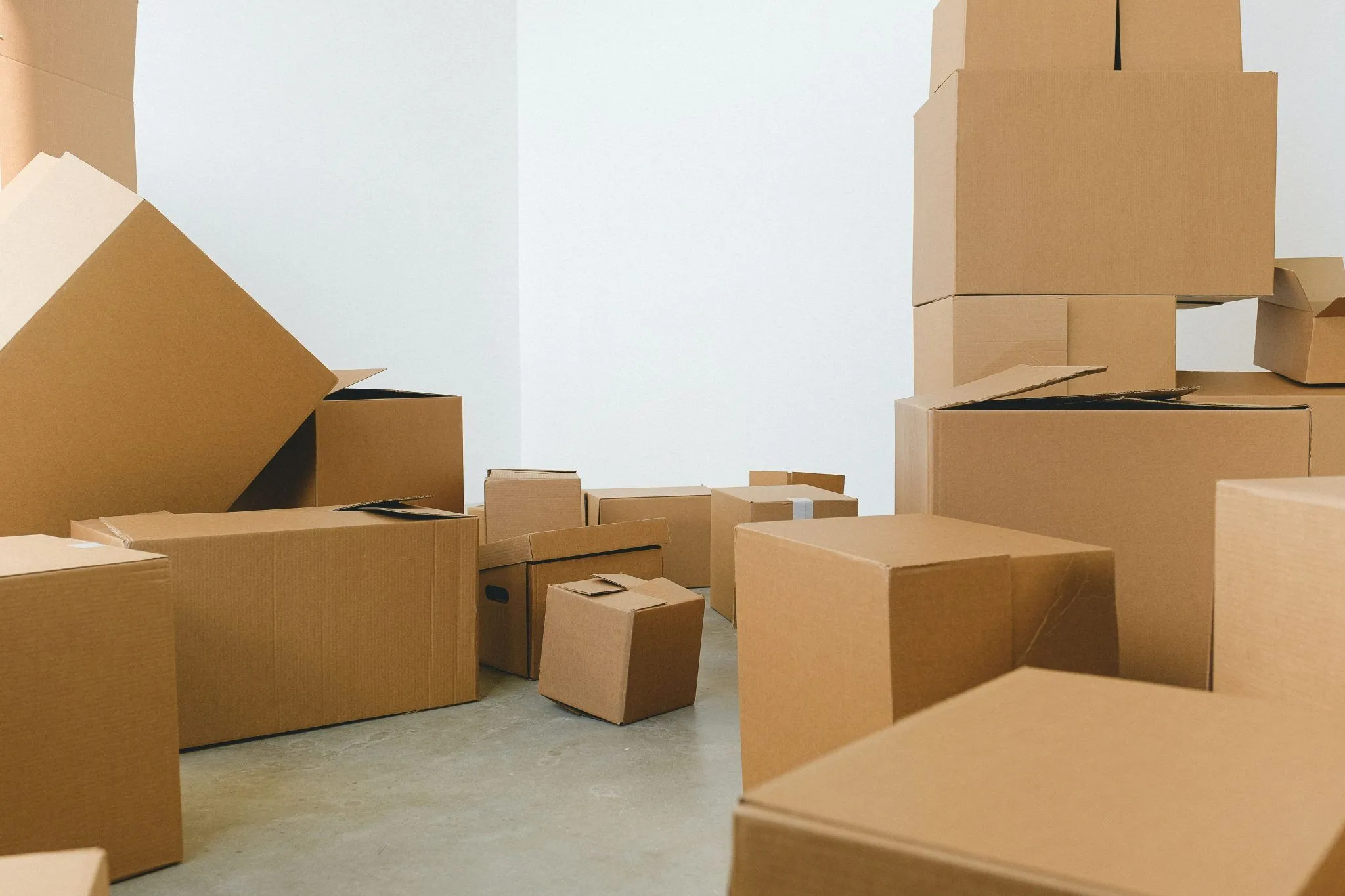
In general terms, it could be said that logistics is the set of all those processes necessary for a product or service to reach the end user; it mainly covers transport, storage and distribution operations.
In turn, and due to the constant change in processes and ways of doing things, largely due to technological advances, different modalities in processes coexist, such as reverse logistics.
La reverse logistics It is a very broad concept that can encompass a myriad of activities since, for example, some of them have ecological purposes (with the objective of avoiding harm to the environment) or others for commercial or productive purposes only, since their actions are interconnected to market supply.
So... What is Reverse Logistics?
With the rise of the already known ecommerce, logistics processes have been forced to adapt and update themselves to new trends and market processes in order to maintain competitiveness vis-a-vis other companies. One of the aspects in which logistics has had to adapt the most due to these b2c stores is, precisely, in the logistics of returns or returns (those users who have purchased an item online and want to return it directly).
In this way, reverse logistics can be defined as the set of practices and processes responsible for managing the returns and returns of those products purchased by users. These returns or returns are managed from the points of sale of the products to the manufacturer itself (to carry out the repair, recycling or disposal of the product at the lowest possible cost).
In addition, logistics is already another process and of vital importance when planning the supply chain for the satisfaction of the end customer.
What are the differences between regular logistics and reverse logistics?
The infrastructure required to manage reverse logistics processes is, as a general rule, the same as for any other logistics process in use. However, we can find differences both in its planning and in its monitoring: the operation is different, since now the customer is the one who can act as a “warehouse” and wait for the collection of their product for subsequent evaluation and economic compensation. In this way, new adapted processes must be considered and taken into account, such as the user's pickup or the treatment of the return product.
Types of Reverse Logistics
According to the article on Reverse Logistics From the company Imatica, specialized in IT services and management software, two types of reverse logistics can be differentiated due to the difference in their approach or objectives.
Business: consists of managing the returns that customers make to inventories or manufacturers.
Eco-friendly: one of the priorities of reverse logistics is precisely the reduction of the environmental impact caused by business activities. For this reason, its use for waste treatment, such as recycling, is also very popular (discarded objects are grouped together for their subsequent recovery process to promote their use).
Benefits of Reverse Logistics
The benefits of reverse logistics are diverse, since they can have both an impact on a better corporate image of the company as well as contributing to a cost reduction. In addition, it is also necessary to highlight the enormous environmental benefit in ecological reverse logistics thanks to practices such as recycling.
Economically, this type of logistics can be significantly beneficial since it is reduced both in time and in costs because there is no need to invest in new materials in the production chain.
Also, and taking into account the typology, “ecological inverted logistics” promotes environmental protection as long as practices such as recycling are carried out (raw materials are created from waste, thus generating a second life cycle for products). All of this also contributes to the improvement of the company's corporate image, since all actions that take advantage of sustainability are increasingly recognized and better valued.
For all these reasons, reverse logistics must be increasingly optimal and efficient, since the management capacity that any company has to manage services such as product returns or customer returns will determine its business success.
As with traditional logistics and last-mile delivery services, reverse logistics also requires tailored planning and optimization, since the user's requirements will be the same: a satisfactory experience both in terms of quality and economy with timely collections and quick returns.
In order to plan reverse logistics that meets the needs of users, it is essential to adopt a last mile management software that allows the efficiency and optimization of all the resources available in your company.
With Routal Planner you will get specialized software that can carry out the different operations that involve reverse logistics, such as the collection and return of products, thanks to optimal planning of the process and with real-time monitoring of its development. Below, we show you a short video in which we show you how to carry out this type of operation in a simple and, above all, efficient way thanks to the use of Planner.
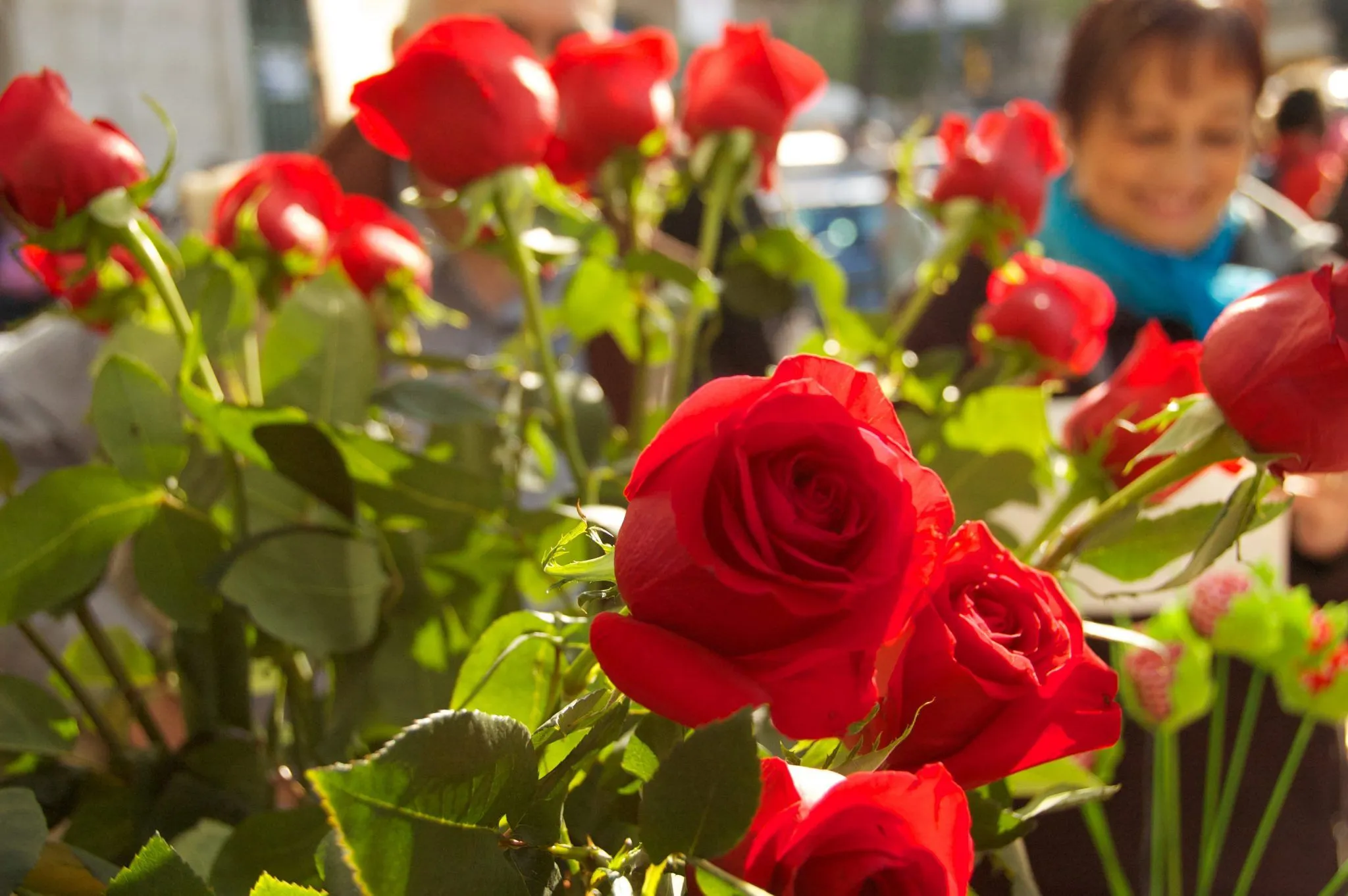
Sant Jordi is always a special day, books, roses, queues and people, lots of people. Everyone is out on the street, enjoying a magical day for both children and adults. It is the day of the year when the most books are sold, 7.5% of annual sales In the city of Barcelona.
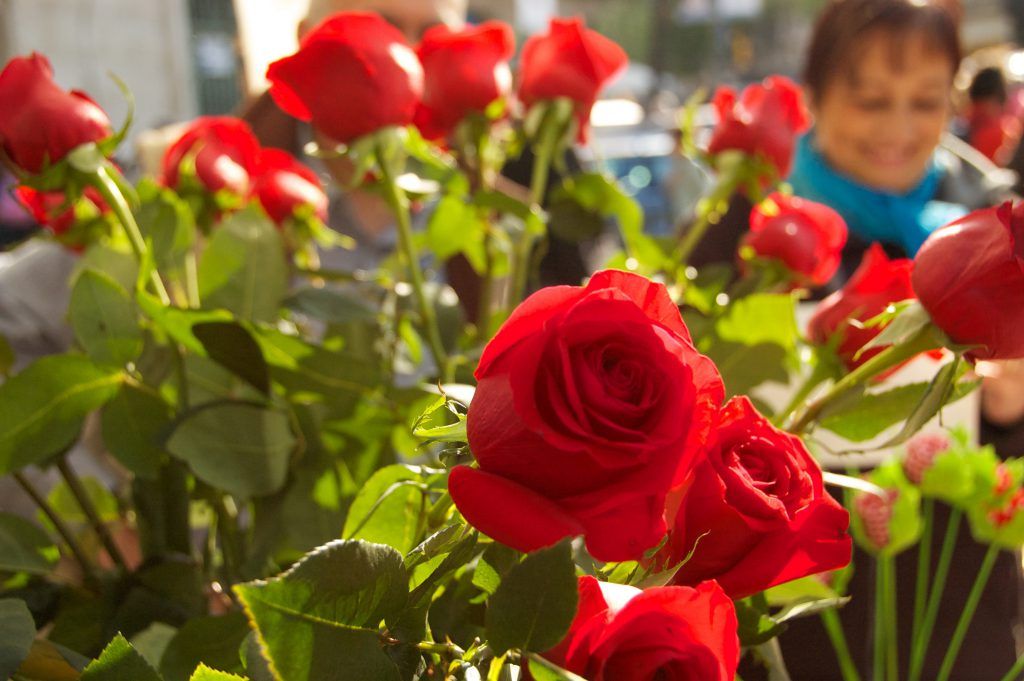
This year will be special. We'll have to spend it at home, enjoying a good read, our recommendation for these days The Black Swan by Nassim Taleb. This year we will save ourselves the hassle of Las Ramblas and we will have to buy the roses online. Without a doubt, a special year.
We want to take advantage of this important date to see the success of initiatives that, in a normal year, would hardly have achieved such overwhelming success.
One of our customers Santjordiacasa.com is using Highway as a tool to optimize the distribution of roses on such a special date as Sant Jordi.
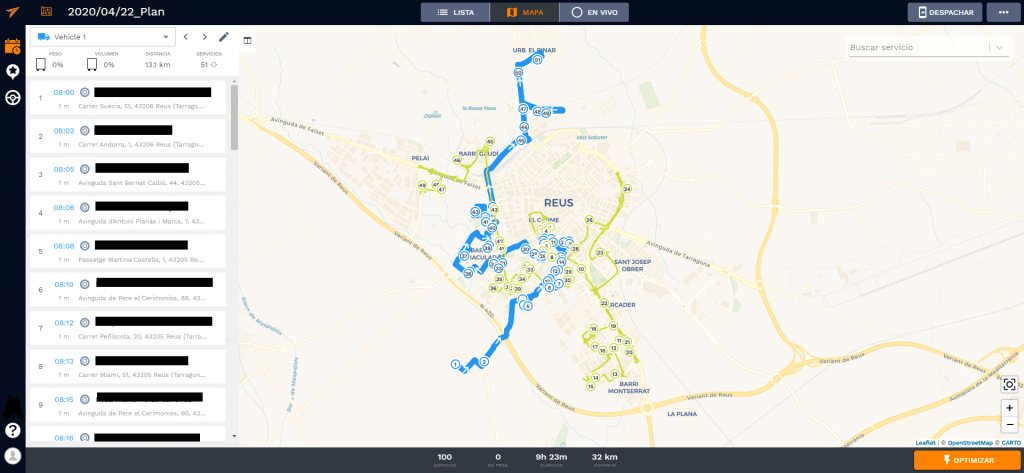
Thanks to the power of the Highway route planner, they have been able to grow in deliveries and reach customers that would have been impossible for them before.
Like them, hundreds of other customers are entering a world such as home delivery. A channel that had often been completely forgotten. Thanks, or unfortunately, COVID-19 has forced the launch of new marketing channels such as Ecommerce and its own distribution and home delivery.
We are seeing this in our traditional customers, distribution companies to the HORECA channel that are converting to home distributors overnight.
Pastry shops such as Cropics they were able to deliver all the Easter monkeys in record time and have the detail of leaving a monkey at my wife's grandmother's house 😁. These types of details make being able to help small businesses make you proud of the work you do and of seeing how you can help more people around you.
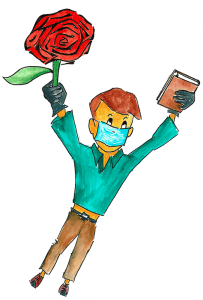
We are in a very difficult time for many companies and families. There is little help to get through this crisis and reaching those people we can help is always a challenge. I encourage you to share our story, the story of our users and customers, companies that are embarking on a new adventure, delivery. Without experience, without processes, but with a desire to fight and face the corona, you are not alone.
We won this together.
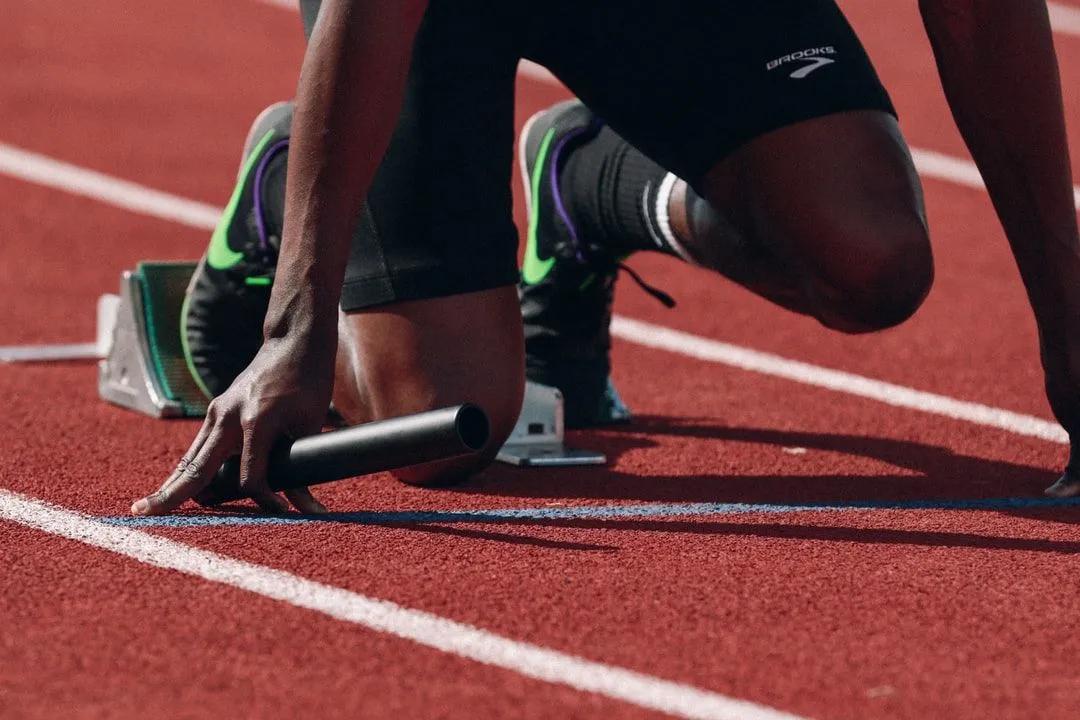
The distribution on demand is an industry that is growing at a very high speed. New companies appear every day, especially in the market for food, beverages and deliveries of perishable products. And the competition is wild. Efficiency is a key metric in the “I want it all and I want it now” era and the most critical part is what happens from when a new order is placed until it is delivered.
Today I want to focus on the problem of sending new orders, that is, how to decide which courier service the order should be assigned to when an order enters the system. This is because the dispatch today is not addressed systematically. Optimizing the dispatch system can minimize delivery time and improve customer satisfaction.
The operating paradigm of companies that deliver on demand can be divided into two different types:
- Operations based on a single warehouse are those operations focused on a single tank. This warehouse has several dealers and the programming is done once to obtain an order list; usually grouping orders by area. Amazon Prime is a good example of this paradigm.
- Operations based on multiple warehouses are those operations that rely on choosing the order in one of the multiple warehouses and delivering it to a customer. In this case, the delivery people are scattered around the city, and once a new order arrives, it is assigned through a shipping process to one of the multiple delivery people. Companies such as Uber, Just Eat, Delivero, etc. operate this way.
The problem of dispatching is solved more or less satisfactorily in the first scenario thanks to the possibility of linking together a list of deliveries and considering it as a Traveling Seller Problem (Traveling Salesman Problem) with some pre-clustering restrictions (OK, I know that TSP is an expensive problem, but... come on, it's about Amazon).
On the contrary, in the second scenario, it is not so clear that the problem is being optimally addressed. How can a new incoming order be added to a running scenario? There are tons of variables to consider:
- Can the courier make multiple collections before starting to deliver?
- Can an already assigned order be reassigned to another courier service?
- Do all orders have the same priority? (for example, all orders must be delivered no later than 30 minutes after placing them)
Do orders need to be delivered by a particular vehicle? - ...
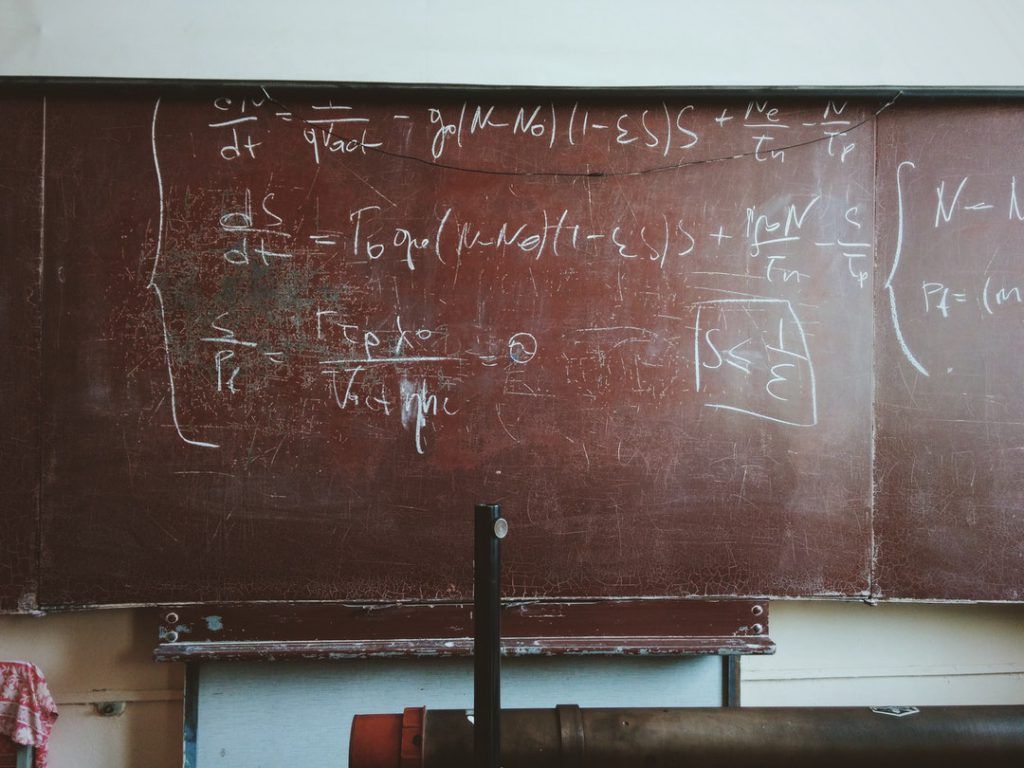
Modeling this scenario can be quite challenging, and that's why SmartMonkey has been working on this problem for a while. We call our solution Online Programming Optimization Model (OSOM) (Yes, branding isn't one of our strengths 😅, but phonetically it sounds like “incredible” and that's pretty fun). OSOM can model business restrictions and find a feasible solution to the dispatching problem.
In the simulation below, we have modeled a world where:
- A courier service can be assigned multiple pickups and deliveries at the same time
- and the first next service of each messaging service is fixed and cannot be reassigned in subsequent iterations.
The visualization contains twenty iterations of the world divided into two steps:
1. New incoming services are marked in gray.
2. Services are dynamically assigned to deliverers to optimize overall delivery time.
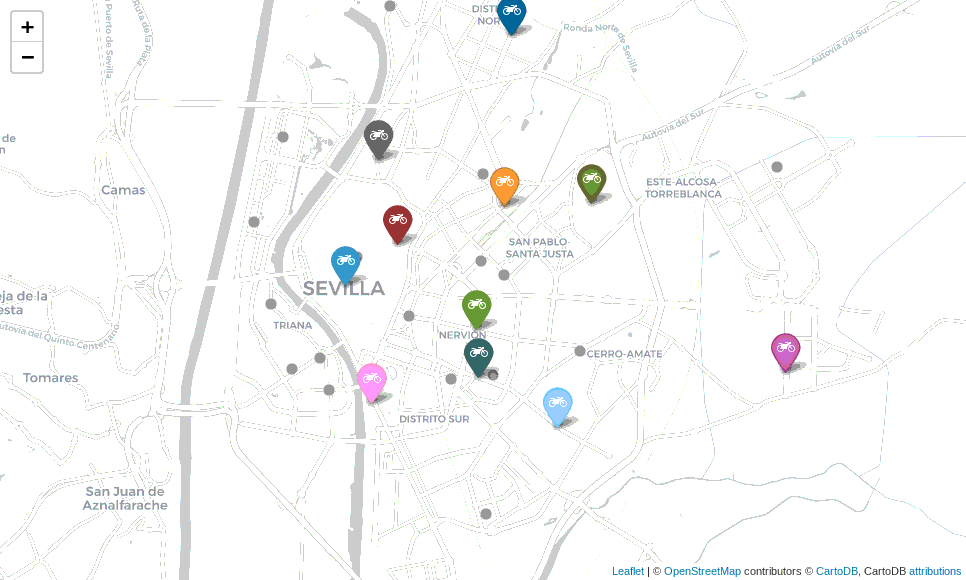