Logistics
%20(5).webp)
La lack of delivery people has become one of the main challenges faced by logistics and distribution companies. According to recent data, more than 90% of companies They have Problems hiring delivery people, directly affecting the efficiency of their last-mile operations. But why are there a shortage of drivers? What solutions are there to mitigate this problem?
In this article, we explain the causes of the shortage of delivery people, their impact on the business and how technological solutions for delivery, like Routal, can help you maintain high performance even in high-turnover settings.
🔍 Why is there such a lack of delivery people?
1. Structural deficit in the sector
In Spain, the logistics sector has a Deficit of 15,000 professional drivers, and the projections are not encouraging at all. This problem has become a threat to the continuity of logistics operations, especially in urban distribution.
2. High delivery turnover
The delivery job, although not underpaid, is physically demanding, stressful and, in many cases, precarious. This generates a high delivery turnover, forcing companies to constantly invest in new selection and training processes.
3. Lack of generational replacement
Only 4.5% of delivery people are under 25 years old. The profession is not attractive to young people, who are looking for jobs that are more technological, flexible or with better working conditions.
4. Labor competence with other sectors
Many people with professional driving licenses prefer to work in public sectors or urban transport companies where working conditions are more stable and predictable.
🛠️ Technological solutions to combat the lack of delivery people
In this context, technology becomes a strategic ally. Platforms such as Routal offer specific tools that allow companies to deal with lack of delivery people without compromising the quality of service.
✅ Route optimization
Thanks to Routal's advanced planning engine, it is possible to assign more efficient routes to each driver. Not only does this reduce total work time, but it also allows for more deliveries with fewer resources. Reducing the need for a large number of delivery people.
✅ Reducing operational stress
With optimized routes, real-time tracking and automatic notifications, drivers have to make fewer decisions under pressure, improving their experience and loyalty.
✅ Higher productivity with less staff
Routal allows maintain high performance even with a small workforce. Automatic analysis tools and reports allow you to detect bottlenecks and adjust operations in real time.
✅ Better communication and feedback
The integration of satisfaction surveys and the total visibility of deliveries generate greater motivation in delivery people, knowing that their work is valued and visible.
🚀 Conclusion: A lack of delivery people doesn't have to slow down your business
La Shortage of delivery people it's real, but It's not a conviction. If your company is experimenting Problems hiring delivery people or suffer from high turnover, adopt a platform such as Routal can make a difference.
Investing in technology not only solves immediate operational challenges, but it also makes the work environment a more attractive, efficient and sustainable place for drivers.
Do you want to see how Routal can help you? 💡 Request a demo and transform your last-mile logistics.
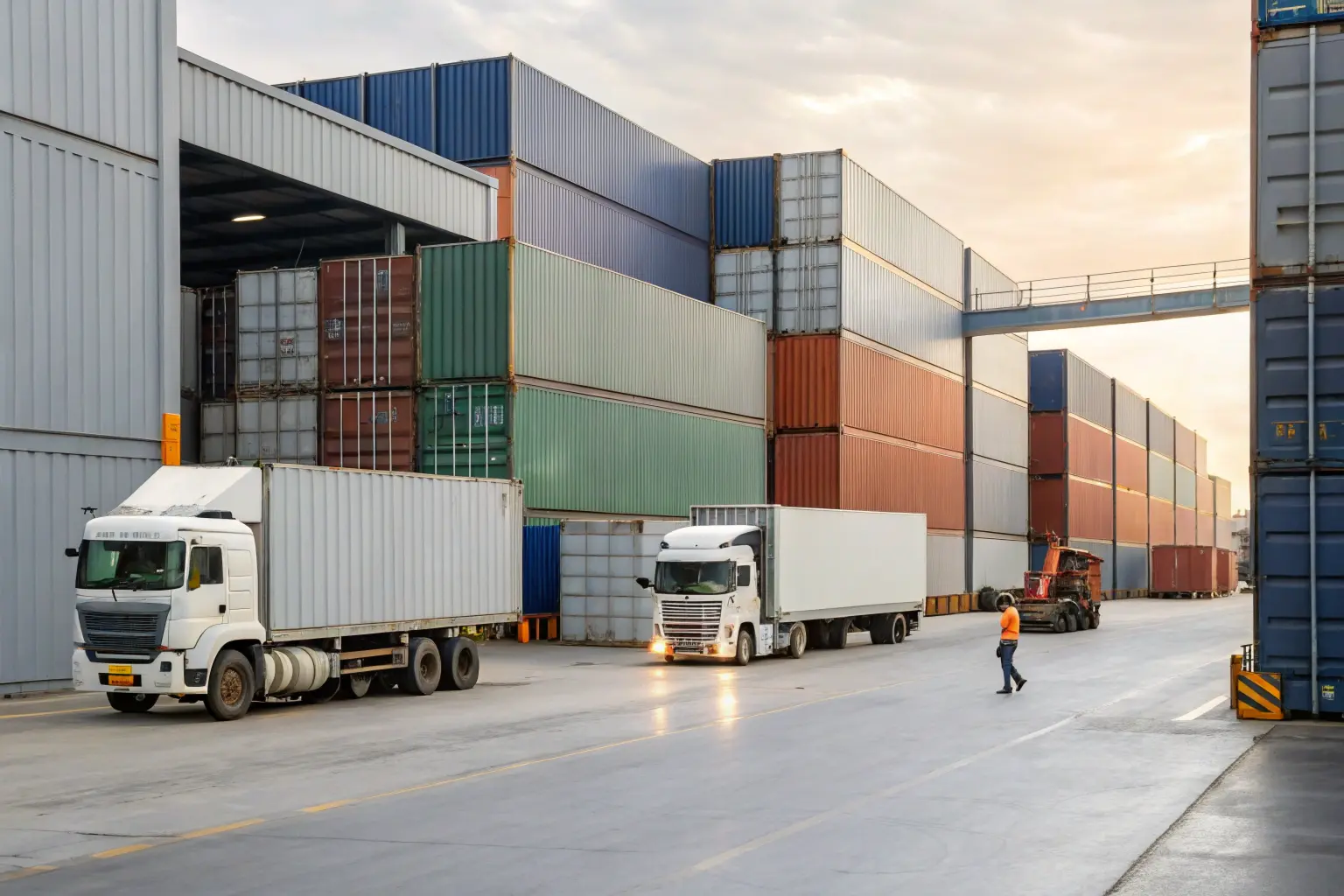
Los logistics operators they play a fundamental role in the supply chain, since they are responsible for manage, coordinate and streamline the flow of goods and services from origin to final destination. Its function can range from basic tasks, such as warehousing and transportation, to the comprehensive management of all the logistics of a company, including technology, consulting and process optimization.
Depending on the degree of integration and control that the logistics operator has over a company's operations, we can distinguish:
1PL Logistics Operator (First Party Logistics - First Party Logistics)
La First Party Logistics (1PL) It is the model in which a company manages its own logistics activities without the intervention of third parties. This means that the company is directly responsible for transporting, storing, distributing and managing its products from their origin to their final destination.
This model is primarily used by companies with great operational capacity who can afford to invest in their own logistics infrastructure.
Key Features of 1PL
Total self-management: The company owns and manages its own logistics resources, such as truck fleets, warehouses and distribution centers.
High initial costs: Requires significant investment in infrastructure and logistics personnel.
Examples of Companies Using the 1PL Model
Coca-Cola:
• The company manages its own distribution network with factories, warehouses and a fleet of trucks to take its products to the points of sale.
Zara (Inditex Group):
• It controls its own supply chain with its own logistics centers and direct distribution to its stores in different countries.
Nestle:
• The company manages its own production and distribution chain in several markets, ensuring the efficient supply of its products.
Advantages of the Model 1PL
Greater control over the supply chain.
Long-term cost reduction (by eliminating intermediaries).
Better time management and quality of service.
Optimization of infrastructure and logistics personnel.
Disadvantages of the Model 1PL
High initial investment costs in infrastructure and vehicles.
Complexity in logistics management (need for experts and advanced technology).
Less flexibility to adapt to market fluctuations
Logistic Operator 2PL (Second Party Logistics)
La Second Party Logistics (2PL) refers to when a company outsourced specific logistics services to a specialized supplier. In this case, The company continues to manage its logistics, but outsources key functions to specialized operators to improve efficiency and reduce costs.
This model is common in companies that do not want to invest in their own logistics infrastructure, but that need to ensure an efficient distribution of their products.
Key Features of 2PL
Outsourcing key services: Companies specialized in transportation, storage or distribution are outsourced.
Focus on operational efficiency: It allows companies to optimize their logistics without making large investments in their own infrastructure.
Functions that a 2PL Logistics Operator can perform
- Freight transport.
- Storage and stock management.
- Loading and unloading management.
- Management of customs and international procedures.
- Multimodal transport (combination of different types of transport).
Examples of 2PL Companies
DHL Freight (land transport):
• Companies that need to move goods nationally or internationally can subcontract to DHL for ground transportation.
Maersk (maritime transport):
• Many manufacturing and foreign trade companies use Maersk to ship goods through containers by sea.
UPS Supply Chain Solutions (storage and distribution):
• Companies that don't have their own warehouses can use UPS fulfillment centers to manage inventories and distribute products.
FedEx Logistics (air transport and cargo solutions):
• Companies that require urgent shipments hire FedEx to make international deliveries by air transport.
GLS, SEUR or MRW (transport and parcel delivery):
• E-commerce or retail companies use last-mile transportation services from operators such as GLS or SEUR to deliver products to customers.
Advantages of the 2PL Model
Lower investment in infrastructure.
Flexibility and scalability.
Access to specialized expertise.
Expansion to new markets.
Disadvantages of the 2PL Model
Less control over the logistics chain.
Possible delivery delays.
Variable costs depending on the volume of operations.
Risk of loss of key information.
Logistics Operator 3PL (Third Party Logistics)
La Third Party Logistics (3PL) It is a model in which a company outsource the complete management of your logistics to a specialized supplier.
Unlike the model 2PL, where only specific functions are outsourced, in 3PL the logistics operator becomes a strategic partner, managing a significant part of the supply chain, allowing companies to focus on their core business while leaving logistics in the hands of experts.
Key Features of 3PL
Total outsourcing of logistics: An external supplier is responsible for the storage, transportation and distribution of products.
Integrated management: The 3PL operator coordinates multiple logistics functions within the supply chain.
Functions of a 3PL Logistics Operator
- Transportation and Distribution Management.
- Storage and Inventory Management.
- Order Preparation (Pick & Pack).
- Customs Management and International Trade.
- Analysis and Optimization of Logistics Processes.
Examples of 3PL Companies
Amazon FBA (Fulfillment by Amazon):
• Companies and online sellers use Amazon's 3PL service to store their products in their fulfillment centers and manage shipping, returns and customer service.
DHL Supply Chain:
• Provides storage, distribution and customized logistics solutions for multiple industries.
UPS Supply Chain Solutions:
• Manages the logistics of retail, e-commerce and manufacturing companies, offering transportation and storage.
XPO Logistics:
• Specialized in storage and transport logistics for industrial and retail companies.
CEVA Logistics:
• It operates globally offering transportation, distribution and storage solutions for technology, automotive and consumer goods companies.
Advantages of the 3PL Model
Reduced operating costs.
Greater efficiency and specialization.
Scalability and flexibility.
Focus on the core business.
Access to advanced technology.
Disadvantages of the 3PL Model
Less control over logistics.
Variable costs.
Risk of supply chain failures.
It can be difficult to synchronize company systems with those of the logistics provider.
Logistics Operator 4PL (Fourth Party Logistics)
La Fourth Party Logistics (4PL) is an advanced model of logistics outsourcing in which a company hires a specialized supplier or consultant for you to manage and optimize your entire supply chain.
Unlike the 3PL, where the operator only functions logistics, in 4PL the supplier is responsible for coordinating different logistics operators (3PL, carriers, warehouses, customs, etc.) to offer a comprehensive solution.
This model is ideal for companies looking for fully optimized logistics management, with the use of technology, data analysis and artificial intelligence to improve efficiency and reduce costs.
Key Features of 4PL
Comprehensive supply chain management: Coordinates and optimizes all logistics processes.
Use of advanced technology: Integration of systems such as ERP, WMS and TMS for analysis and decision-making.
It has no physical assets: It does not operate its own warehouses or fleets, but rather manages 3PL operators and other logistics providers.
Optimization and strategy: Focuses on improving costs, delivery times and operational efficiency.
Consulting-based model: Provides strategic analysis and recommendations for the supply chain.
Functions of a 4PL Logistics Operator
- Management and Coordination of Logistics Providers (3PL, Carriers, Customs, etc.)
- Data Analysis and Supply Chain Optimization
- Strategic Planning and Logistics Consulting
- Technological Integration and Digitalization of Logistics
- Risk Management and International Logistics
Examples of 4PL Companies
Accenture Logistics & Supply Chain Management:
• Offers consulting and supply chain optimization services for large companies.
DHL Supply Chain 4PL Services:
• Manages and coordinates multiple logistics providers for global companies, optimizing costs and delivery times.
XPO Logistics (4PL Division):
• Provides integrated solutions for the planning and logistics execution of large corporations.
UPS 4PL Solutions:
• Integrates the management of logistics operators and carriers into a single, optimized solution.
GEODIS Supply Chain Optimization:
• Specialized in logistics consulting and data analysis to improve the supply chain of its customers.
Advantages of the 4PL Model
Total optimization of the supply chain
Cost reduction and service improvement
Increased visibility and control
Long-term strategy
Increased flexibility and scalability
Disadvantages of the Model 4PL
Less direct control
High initial costs
Technology Dependency
Not suitable for small businesses
Logistics Operator 5PL (Fifth Party Logistics)
La Fifth Party Logistics (5PL) represents the most advanced level of logistics outsourcing, where an operator not only manages and optimizes the entire supply chain as in 4PL, but also integrates multiple logistics networks and advanced technologies for total automation and efficiency.
The operators 5PL focus on digitalization, artificial intelligence, big data and the optimization of global logistics, especially in sectors such as e-commerce, retail, manufacturing and international logistics.
Unlike the 4PL, where the supplier acts as a strategic supply chain manager, in 5PL the operator designs complete logistics ecosystems and uses state of the art technology to automate processes and optimize costs on a large scale.
Key Features of 5PL
Automation and total digitalization: Use of artificial intelligence, machine learning, IoT and blockchain to manage the supply chain.
Integration of global logistics networks: Coordinates multiple logistics operators (3PL, 4PL, carriers and technology providers).
Optimization based on Big Data: Analyze data in real time to improve efficiency, reduce costs and forecast demand.
Technology-based business model: It focuses on software, digital platforms and automation rather than its own physical infrastructure.
Functions of a 5PL Logistics Operator
- Optimization and Management of the Global Supply Chain
- Use of Artificial Intelligence and Machine Learning
- Blockchain and Supply Chain Security
- Sustainable Logistics Strategies and Green Logistics
- Warehouse Automation and Last Mile
Examples of 5PL Companies
Alibaba Logistics Network (Cainiao):
• Cainiao optimizes Alibaba's entire supply chain using big data, artificial intelligence and advanced automation.
Amazon Robotics & Fulfillment Services:
• Amazon deploys robots, drones and artificial intelligence systems to manage logistics on a global scale.
Flexport:
• Digital logistics platform that combines technology, artificial intelligence and blockchain to optimize the international supply chain.
Kuehne + Nagel Integrated Logistics:
• It offers digital logistics solutions based on big data, machine learning and automation.
DHL Smart Logistics Solutions:
• Develops logistics systems based on IoT, automation and big data for global customers.
Advantages of the Model 5PL
Full automation of the supply chain.
Reduction of operating costs through the use of AI and Big Data to optimize each logistics process.
Greater security and traceability through the implementation of blockchain and intelligent systems.
Greater flexibility and scalability.
Sustainability and resource optimization.
Disadvantages of the Model 5PL
High initial investment in technology.
Technological dependence.
Less direct control over logistics
Complexity in implementation.
.webp)
The logistics department is the operational heart of any company that handles distribution, transportation or merchandise management. Its importance lies in ensuring that products arrive at the right place, at the right time and with the most efficient costs. But what exactly does this department do? What are the profiles that make it up? In this article, we'll explore their key functions and main roles.
What is the logistics department?
The logistics department is responsible for planning, executing and overseeing the movement and storage of goods, services and information along the supply chain. This includes activities such as inventory management, designing transportation routes, and coordinating with suppliers and customers.
The main objective is to optimize processes to reduce costs, improve time and ensure customer satisfaction.
Main functions of the logistics department
1. Supply chain planning
This team ensures that every step of the logistics process is aligned with the company's goals. It focuses on anticipating demand, managing resources and avoiding bottlenecks.
2. Inventory Management
Controlling inventory is crucial to avoid unnecessary costs, such as excess stock or lack of products. This includes monitoring stock in real time and maintaining the perfect balance between supply and demand.
3. Transportation and distribution coordination
Ensuring that products arrive at their destination efficiently is essential. This involves designing optimal routes, choosing the right means of transport and managing deliveries.
4. Relationship with suppliers and customers
The logistics department acts as an intermediary between the company and its business partners. Negotiate deadlines, prices and terms with suppliers and ensure end customer satisfaction.
5. Process analysis and optimization
Measuring performance and finding areas for improvement is a constant function. This includes the use of technological tools such as Routal to optimize routes and reduce operating costs.
Main profiles in the logistics department
The logistics team is usually made up of professionals with both technical and organizational skills. The following are the most common roles:
1. Logistics Manager
Responsible for overseeing the entire department, from strategic planning to the execution of operations. He is the one who makes key decisions to ensure that processes work efficiently.
2. Transportation Coordinator
Responsible for planning routes, managing fleets and ensuring that shipments arrive on time. Their work is essential to reduce costs and meet deadlines.
3. Logistics Analyst
This profile focuses on analyzing data and metrics to improve processes. It uses technological tools to identify areas for improvement in the supply chain.
4. Inventory Manager
It ensures that inventory levels are adequate, minimizing storage costs and avoiding stock breaks.
5. Customer Care Specialist
Work directly with customers to resolve issues, manage returns and ensure a positive experience.
Technology as an ally of the logistics department
Currently, tools such as Routal are essential for logistics departments. By optimizing transport routes, automating planning and providing real-time analysis, they allow teams to work more efficiently and focus on strategic tasks.
Conclusion
The logistics department is a key part of any company that manages products. Its functions go beyond transportation; they involve strategic planning, constant analysis and customer service. In addition, the profiles that make up this team provide unique skills that allow each link in the supply chain to work perfectly.
With appropriate technological tools, such as Routal, the success of this department is more assured than ever.
Is your company looking to optimize its last-mile logistics?
Find out how Routal can help you reduce costs, improve delivery times and increase customer satisfaction. 🚛✨
Suggested image
A modern design that represents a logistics team in action, showing a combination of technology and human work. Ideally, an on-screen digital map, an organized warehouse, and people planning routes or supervising processes.
What do you think? Would you add more profiles or functions? Write to us in the comments.
%20(1).png)
Transportation route management is a key process in modern logistics, especially in the last mile, where every minute counts to meet customer expectations. From picking to final delivery, every step in the chain can present challenges that impact efficiency. In this article, we will analyze each stage of the process, the associated challenges and how tools such as Routal can transform the management of transport routes into an agile and effective operation.
1. Picking and order preparation
Picking is the first step in managing a transport route. It involves selecting the right products in the warehouse to fulfill a specific order. Efficient preparation ensures that products are ready for shipment in the shortest possible time.
Common Challenges:
• Errors in product selection.
• Lack of synchronization between warehouse and transport.
• Time-out in order preparation.
Solution with technology:
With a tool such as Routal, you can integrate inventory management systems to synchronize order preparation with route planning. In addition, allocations can be optimized to ensure that orders are ready just in time for transportation.
2. Route planning
Designing optimal routes is at the heart of transport management. It involves organizing destinations in an order that minimizes travel times and reduces costs.
Common Challenges:
• Unexpected traffic or adverse weather conditions.
• Last-minute changes to orders or addresses.
• Lack of visibility on the condition of vehicles and drivers.
Solution with technology:
Routal uses advanced optimization algorithms that consider factors such as real-time traffic, delivery restrictions and vehicle capacity. Not only does this reduce the kilometers traveled, but it also improves on-time deliveries.
3. Transportation and final delivery
Once en route, the final delivery represents direct contact with the customer and is often the most critical moment.
Common Challenges:
• Difficult location of destinations.
• Customer frustration due to delays or lack of communication
• Accessibility issues in certain areas.
Solution with technology:
With Routal, drivers can access detailed and updated maps, receive notifications of changes in real time and communicate with customers directly through the platform. In addition, customers can track their order and receive alerts about the estimated time of arrival (ETA).
4. Real-time monitoring
The ability to monitor routes in real time is key to identifying problems and solving them before they affect the customer experience.
Common Challenges:
• Lack of visibility on the delivery status.
• Slow response to incidents such as delays or breakdowns.
Solution with technology:
Routal offers a centralized platform where managers can monitor the progress of each delivery in real time. With this information, it is possible to redirect routes, reassign orders, or proactively inform the customer in case of delays.
5. Communication with the recipient
Clear and timely communication is critical to ensuring a satisfying customer experience.
Common Challenges:
• Lack of updates on order status.
• Difficulty coordinating deliveries at specific times
Solution with technology:
Routal allows you to automate messages to keep customers informed at every stage of the process. From the time the order is picked up until it is delivered, customers can receive personalized notifications that keep them in the know.
General challenges in managing transport routes
• High operating costs due to inefficient routes or downtime.
• Rising customer expectations, especially in fast and traceable deliveries.
• Environmental impact, with increased pressure to reduce the carbon footprint in transport.
How Routal transforms route management
With Routal, every stage of the process is designed to work in sync. From route optimization to customer communication, Routal offers comprehensive solutions that improve operational efficiency and increase customer satisfaction.
• Cost reduction: Shorter routes and faster deliveries.
• Full visibility: Real-time data to make informed decisions.
• Task automation: Less administrative burden and more time to focus on strategy.
Optimizing transport route management isn't just a competitive advantage, it's a necessity in a constantly evolving market. Are you ready to take your logistics to the next level?
Discover how Routal can be your perfect ally. 🚀
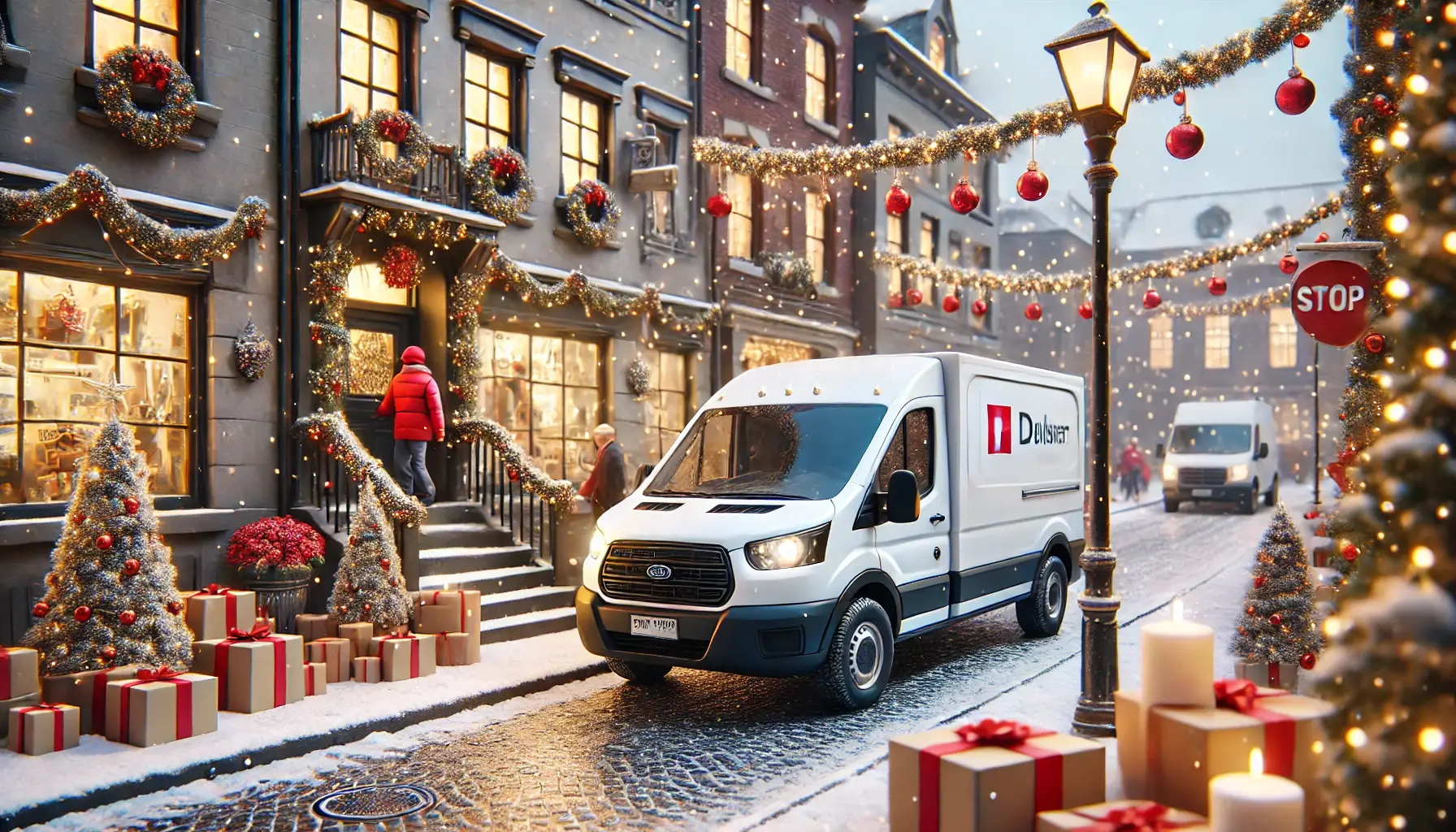
The holiday season is the Super Bowl for courier and parcel companies. Every year, the increase in demand tests the capacity of logistics operations, creating challenges that range from finding temporary staff to meeting timely deliveries to increasingly demanding customers. But all is not lost: a route optimization and communication system such as Routal may be the key to overcoming this stage efficiently and successfully.
The challenges of the Christmas campaign
During Christmas, logistics operations face several specific challenges:
1. Exponential increase in demand: The number of packages can triple or quadruple, creating enormous pressure on operating equipment.
2. Recruitment of temporary staff: It is common to rely on outsourced workers with little experience, which can lead to delivery errors or delays.
3. Customer Expectations: Consumers expect to receive their packages before the specified dates and any error creates major trust problems.
4. Pressure for short times: With tight delivery times, every minute counts.
How optimization software can save the day
A system such as Routal not only does it help to deal with these challenges; it also allows logistics operations to be more resilient, ensuring efficient performance even in the most demanding times. Here's how to:
1. Route optimization for greater efficiency
With a massive increase in shipments, planning efficient routes is crucial. Routal uses advanced algorithms to generate routes that:
• They minimize time in transit.
• They reduce costs by optimizing fuel consumption and vehicle use.
• They adapt in real time to factors such as traffic or weather conditions.
Not only does this benefit experienced drivers, but it also makes it easier for storms to work by providing them with clear, easy-to-follow routes.
2. Support for inexperienced staff
The incorporation of outsourced workers is a lifesaver during the Christmas campaign, but their lack of familiarity with the processes can be a problem. Routal mitigates this risk by:
• Provide intuitive and easy-to-use tools.
• Provide real-time monitoring for supervisors, who can monitor progress and correct errors quickly.
• Integrate detailed guides into the mobile app to ensure that every driver knows exactly what to do and where to go.
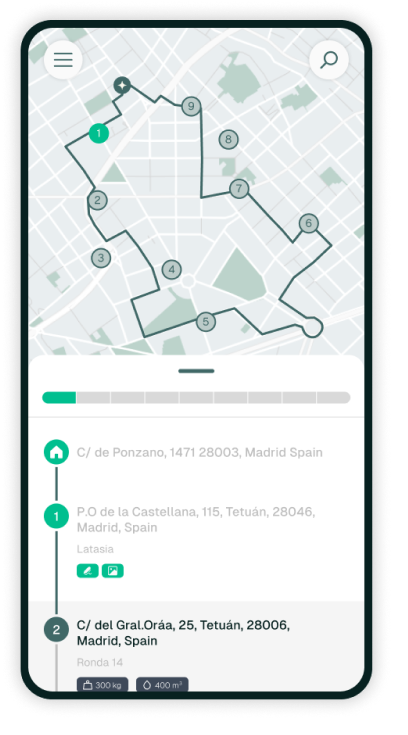
3. Transparent communication with customers
Customer satisfaction largely depends on knowing when your package will arrive. The system of Accurate Routal communication provides:
• Automatic updates on the status of the shipment.
• Reliable and accurate ETA (estimated time of arrival) based on real-time data.
• Notifications of any changes or delays, keeping customers informed at all times.
This reduces the volume of customer service inquiries and builds trust in the brand.
4. Year-round operational resilience
Although Christmas is the toughest test, the tools you adopt to survive this season also improve your operation the rest of the year. By implementing robust software like Routal, you'll be prepared for any peak in demand, whether it's Black Friday, Mother's Day or flash promotions.
Ready for any challenge
Surviving the peak of Christmas requires more than just effort: you need a well-designed strategy and the right tools. With Routal, you not only optimize routes and improve communication; you also strengthen the resilience of your operations, ensuring a constant level of efficiency regardless of the season.
If you want your company not only to survive, but to shine during the Christmas campaign, Routal can help you with this challenge. It's time to transform chaos into control!
We will be happy to hear your challenges and help you throughout the process, Contact us here!
.png)
Last-mile logistics is a business of cents and seconds, every cent counts, every second matters. Making your deliveryman's life more agile, simple and efficient will have a bigger impact than you may be aware of.
Surely you are looking for an app, and just thinking that you will have to explain to all the delivery people how to install it, if it will work on their phones, especially that of external distributors that change every day, among many other problems... you will think that paper is not such a bad solution.
Perhaps there are alternatives other than an app that requires installation, which will be even faster and more convenient than handing over a paper. We are going to see the big differences between a native app, a webapp and finally paper.
.png)
In any change, it is important to identify the main aspects that will mark the success of the change. When adopting a digital solution for delivery people, it is important to reflect on 3 aspects:
- Installing the tool
- The training of the tool
- The adoption of the tool.
Installing the tool
Before deciding on a tool, it is important to thoroughly study the installation process of the chosen tool. A native app will require knowledge on the part of the user when installing apps. Browse the different app stores, until you find the right one. Finally, share with the user their credentials (username and password) in order to access their account. This process must be repeated with all the delivery people, and you will probably have a high turnover, so it will be a process that must be done on a regular basis.
The Routal webapp allows you to speed up this entire process with simple access to a link sent by email, WhatsApp or any other means. It is a very simple and convenient system, especially in companies that work with outsourced services for their operations and these can change daily.
In addition, one of the risks of native apps is support for different models. There are more than 24,000 different models on the market and it's virtually impossible to support all of them. On the contrary, a webapp like Routal's is based on standard HTML code supported by all devices in their native browser. There's nothing worse than hearing a delivery guy say, it doesn't work on my cell phone.
Formation
Training is a key step in using any tool. In general, all mobility tools are usually easy to use by field workers, delivery people, or any employee.
In this video you can see how simple the Routal application is. It doesn't take our customers more than 3 minutes to teach their delivery people how it works.
Adoption
Adopting tools is the most difficult task in any company. Changing the status quo (the company's usual way of working) can be a big challenge. To be successful in this type of project, there is a secret: Generate more convenience to users with the new process.
The application must save time, be simpler than the current solution and, above all, it must make life easier for the worker.
For example, in the Routal webapp, you have a button for direct access to Google Maps or Waze that will fill in the address and guide the delivery person to the delivery point in a single click. Saving a few seconds of copying the address, with the possible errors you may make.
One of the tasks that delivery people do the most is answering the phone. Making calls to customers, receiving calls from their manager to know the status of deliveries, and a long time. Saving 30 seconds by copying a customer's phone number may seem insignificant, but if that task is repeated dozens of times throughout the day, we may be talking about savings of more than 20-30 minutes. Time that can be spent making more deliveries, or avoiding an accident.
Another advantage of digitalization is the ability to share information in real time asynchronously. For example, the status of the deliveries, or the photographs themselves, allow customers and managers to be aware of the status of their delivery and everything that happened at the time they need it. Without bothering, or having to wait. Real-time information, better decisions and more convenient service.
In conclusion, a simple tool that improves the performance of delivery people and is more convenient than the current solution are the keys to achieving the success of a delivery monitoring project.
I encourage you to try our solution Routal Planner route optimization, delivery monitoring through a webapp and real-time communication with your customer.
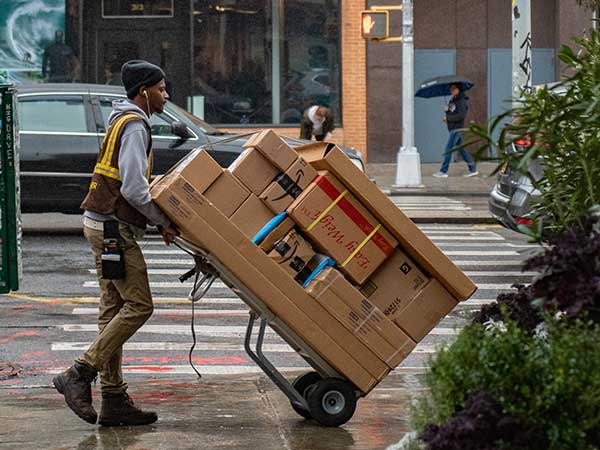
La expectation of a customer versus a service is based on their previous experience and the promise they made to them at the time of purchase. Managing that previous (not necessarily good) experience with the promise of service will mark the success of the service.
Trust is based on complying with the agreement we make with our client. For example, Koiki and its sustainable commitment. Building a trusted service can take years of hard work. Losing that trust, on the other hand, can only mean a bad response from one of our collaborators.
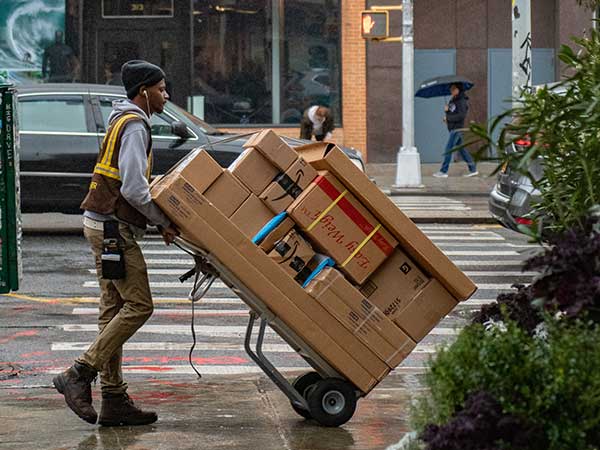
In the world of last mile deliveries, customer expectations are based primarily on these 4 points:
- Delivery time: Customers usually expect their order to be delivered within the agreed time frame. If the order is not delivered in the expected time, the customer may be frustrated.
- Product status: Customers expect the product to be in good condition upon delivery. If the product is damaged or in poor condition, the customer may feel dissatisfied.
- Deliveryman's treatment: Customers expect friendly and professional treatment from the delivery person. If the delivery person is rude or unfriendly, the customer may feel upset.
- Ease of tracking: Customers often expect to be able to track the progress of their order and know their location at all times. If there isn't an easy way to do this, the customer may feel worried or uncomfortable.
Expectation: “Delivery in a timely manner”
For every logistician, that's the goal. Deliver at the agreed time (not earlier and certainly not later) and in the right way. The forms, in many cases, are almost more important. They mean the image of the brand, the relationship with the customer, the condition of the product that you have taken care of throughout the trip. Details, which may seem insignificant, although in many cases they make a difference, and on many occasions the customer is willing to pay for it.
The problem is when the expectation is not met, it can generate frustration in the individual. Frustration is a negative emotion that occurs when a goal is not achieved or when obstacles are found to achieve it. Putting ourselves in the shoes of our customer can help us identify areas for improvement in our service.
Some potential causes of customer frustration include:
- Lack of control: When someone has no control over the outcome of a situation, they may feel frustrated. For example, if a customer expects their order to be delivered within a certain time frame and it doesn't arrive on time, they may be frustrated that they don't have control over the delivery process.
- Lack of information: A lack of information or clarity in instructions can lead to frustration. For example, if a customer doesn't know when their order will arrive or how to track the progress of their delivery, they may be frustrated.
- Lack of support: When someone doesn't receive the necessary support to achieve a goal, they may feel frustrated. For example, if a customer expects to receive care and help from the delivery person and doesn't receive it, they may be frustrated.
For this reason, it is essential to have tools that allow us to properly manage customer expectations. Having control over operations at all times allows us to know if service commitments with the customer are being met. Sharing this information with the customer allows the customer to adapt to a problem. There's no worse feeling than waiting for someone without knowing when they'll arrive. It can be 5 minutes, or 5 hours. This ignorance generates anxiety and in a hyperconnected society it generates a poor customer experience.
If you feel that your operations can improve and that your customers often have the perception that the service they receive is not very good, and you are willing to lead the change in your organization, we recommend that you try Routal Planner. This tool helps companies like yours to offer a more convenient service, save time and logistics costs while empowering customers with information. ¡Take a look here and see for yourself!
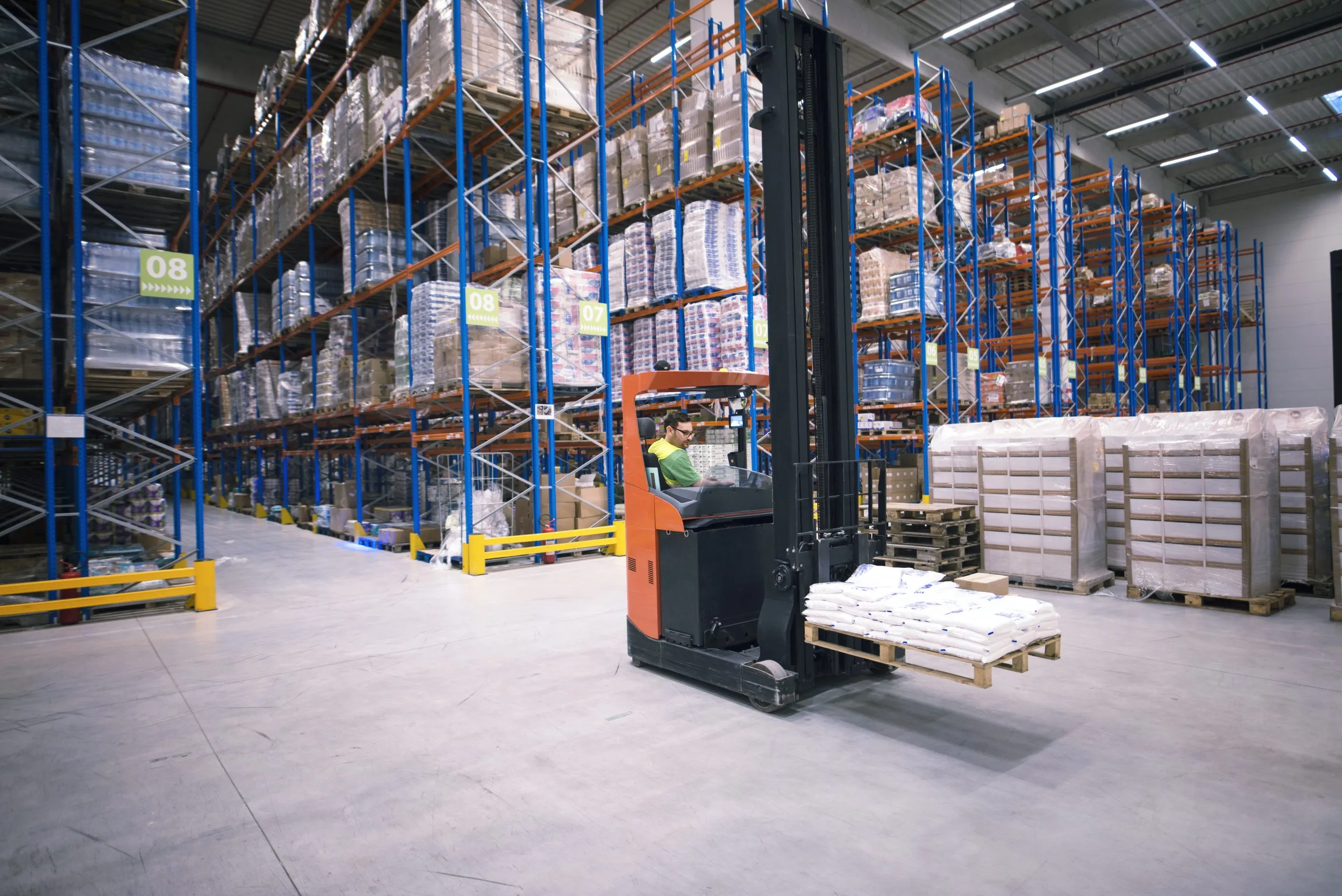
The logistics industry is constantly changing, both in processes and in the way of proceeding. These changes are due, to a large extent, to technological advances in the sector, which evoke different modalities in logistics processes, such as reverse logistics.
What is Reverse Logistics?
Reverse logistics is the set of practices and processes responsible for managing the returns and returns of those products purchased by users.
These returns or returns are managed from the points of sale of the products to the manufacturer itself (to carry out the repair, recycling or disposal of the product at the lowest possible cost).
In addition, reverse logistics is already another process and of vital importance when planning the supply chain for the satisfaction of the end customer.
Reverse logistics is one of the main challenges faced by the industry and the main objective is to avoid high costs and manage returns in the shortest possible time.
8 tips to improve your reverse logistics
Customer Centric: It responds to the customer-oriented strategy through which an organization places the customer at the center of the company with the objective of focusing all processes and operations on users.
The implementation of the Customer Centric strategy increases the satisfaction of our users, since we focus all our efforts on knowing their needs and concerns regarding our activity. Knowing the desired delivery and return times or a maximum price per service will help increase your satisfaction and, therefore, carry out a satisfactory reverse logistics process.
Strategic Planning: Perform measured and analytical planning to ensure the correct management of operations taking into account parameters such as mileage or travel time. With the right software, this will be an autonomous task, in which a large amount of time is not required and with an optimal result, since it will always offer the most efficient route.
Optimization of resources: The optimization of resources when it comes to transportation is essential for the success of your company's reverse logistics process; it will help control the traceability, trajectory and tracking of shipments. In addition, planning delivery routes efficiently and optimally will result in significant economic and time savings. Therefore, the use of specialized software for route planning will be a key element in increasing the efficiency of your company's reverse logistics process.
Use of metrics and KPIs: To evaluate the productivity and performance of the reverse logistics process, the use of KPIs is essential (Key Performance Indicator). These indicators will help measure and quantify your company's performance and compliance with established objectives. It is recommended that when defining the logistics KPIs, they are developed based on the S.M.A.R.T. (Smart, Mmeasurable, Achivable, Realistic and Time-Bound) model.
Shorter return times: As mentioned before in relation to the Customer Centric strategy, it is essential to know not only the limits of our company in terms of acceptable delivery or return times, but also the “deadlines” or desired deadlines of our customers. For this reason, and in general terms, it should be prioritized that collection and return times are as short as possible and without the need to increase the amount of resources associated with reverse logistics. Thus, specific efforts should be made to improve this particular process.
Proactive monitoring: Proactive monitoring is the live monitoring of the daily planning of services and deliveries that warns of possible failures and errors while allowing us to react and adapt operations in a satisfactory manner.
Good proactive monitoring must have the possibility of monitoring the operation in real time and thus be able to view the progress of the operation live at all times. In addition, and in relation to the real-time monitoring of operations, it is essential that it incorporates sufficient functions that allow a timely reaction to possible failures or errors.
Smart Warehouses or Smart Storage: Smart warehouses are specialized logistics centers that make use of technology to increase efficiency in all their processes, such as the reception, preparation or storage of goods.
An example of the use and benefit of implementing intelligent warehouses in the reverse logistics process is the case of Amazon, a company that has included artificial intelligence in its warehouses in order to quickly determine, based on the costs of each product and its associated return costs, if it accepts to pick up the product in question by activating the reverse logistics process or, on the contrary, makes the refund without the collection of said merchandise.
Logistic software: Investing in technology and digitalization can help you improve your reverse logistics efficiently. Choose specific software that includes route optimization, real-time operational monitoring and analysis of important metrics for your continuous improvement.
If you want to guarantee the success of your company's reverse logistics process, you can do so now with specialized software. Routal Planner. Try it now for free by 10 days.
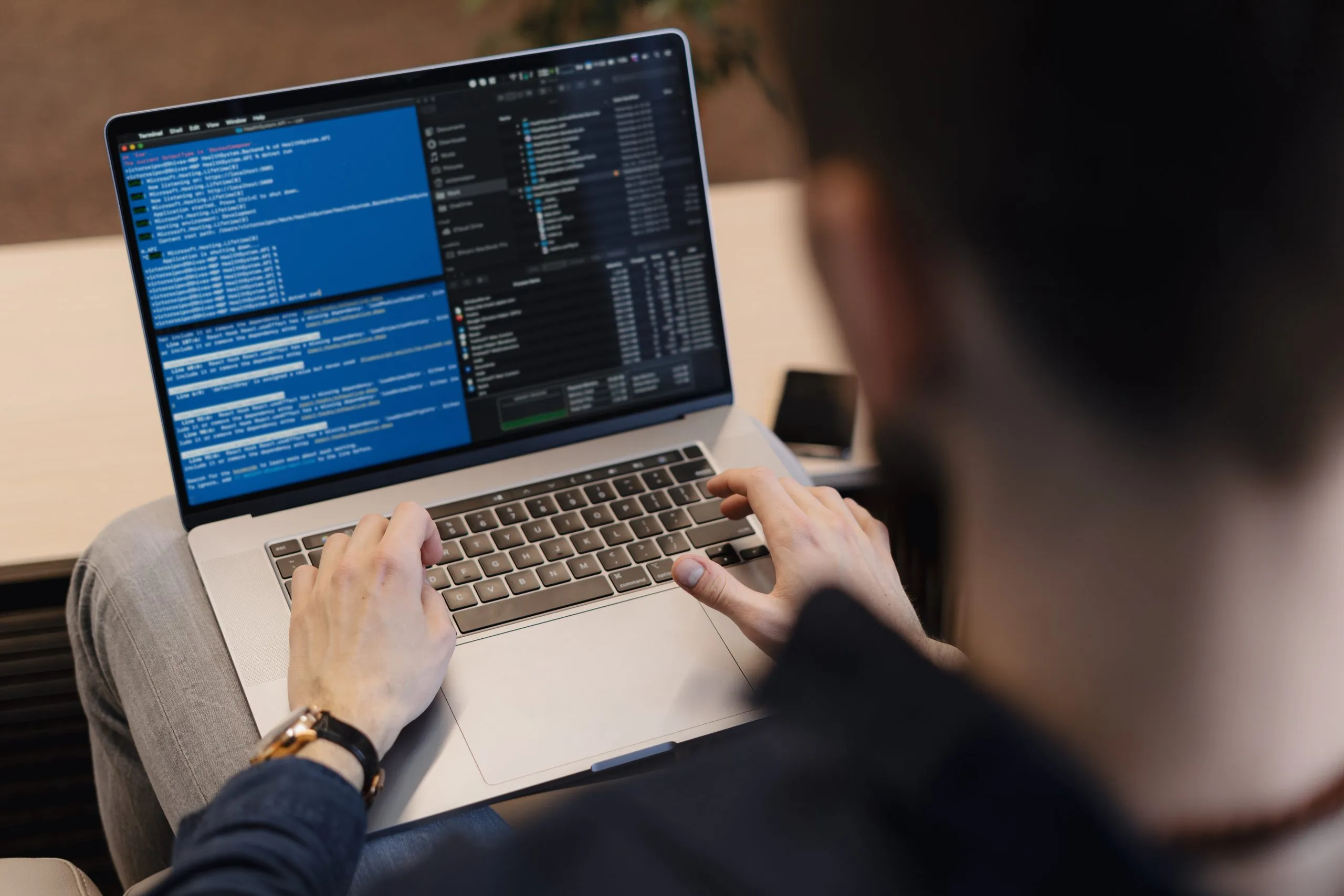
One of the main fears and brakes faced by SMEs in the face of digitalization is Integrate technology. The dichotomy between choosing an all-encompassing solution, or specific solutions for each problem. The benefit of the first option is that you're dealing with a provider, everything is talked about, and you shouldn't have too many problems. The problem is that it probably doesn't solve your processes in the best way and you have to make a lot of effort to adapt your business to the solution. The other option, small experts, usually provide a better solution for each process, but there is a difficulty in getting applications to talk to each other. This means that two companies collaborate, integrate and that can be a challenge.
More complex systems and technological solutions are increasingly required to optimize operations. The trend of one-fits-all (one solution for everything) is increasingly difficult to find and as companies grow they require more specific solutions, so integration projects are becoming more common, but above all, more necessary.
To give great examples, one of Inditex's great successes has been to have a single centralized stock between warehouses and stores, which allows us to have the status of each of the pieces of clothing in real time and achieve greater success in an omnichannel environment where the customer purchases online, is sent from several centers to be consolidated in the store and for the customer to pick up at the store buying an accessory that he found by chance. But something like that is not only available to large companies, SMEs also have a lot to say, and their scale makes them projects much easier, faster and cheaper to implement.
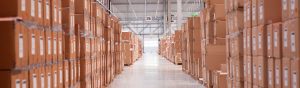
The benefits of integrating systems are direct improvements in productivity and in the quality of the service they provide, standardized and optimized operating processes, ease in internal processes, reduction of errors and also homogenization of data.
Why is it presented as a brake or challenge, or Why does it bring so many headaches for companies? Mainly because many companies do not have the experience, the resources to develop these projects internally or personnel with the knowledge to lead a project of this type. The solution, outsourcing these projects, and without good advice the project can be a big headache. For this reason, looking for a supplier who knows the business, the tools to be integrated and who has experience in similar projects are the key to success for an integration project to be successful, to develop quickly and on budget.
Unfortunately, sometimes digitalization brings high costs that companies don't want to face because of the doubt if there will really be a return on that investment. Digitalization with common sense, improving and streamlining processes undoubtedly generates great investment returns. For this reason, it is essential that companies have an orchestrator that understands the need of the business, the company's processes and those points that hold back the organization in order to optimize them through digitalization. The partner will actually implement that improvement, but it requires high-level coordination that will be the key to success.
Strategy, knowledge and execution.
Nowadays, execution is the easiest part of all. There are different types of integrations depending on the available systems and the objective. The most used are those of APIS (Application Programming Interface) where data is transmitted from one side to the other quickly and securely. It is the most used since it is simpler to perform and offers great performance. These are used to enter information to our platform. On the other hand, the most used to extract information is integration by Webhooks, in which the external system receives data when there is an event on the platform.
At Routal, we are constantly working to make integrations an opportunity to further streamline company processes, digitize and automate tasks that don't add value, and concentrate the work of employees on those points where a person actually provides the most value.
Quaker State Success Story: Integrating SAP
Quaker State is a leading company in the distribution of oils and lubricants for vehicles in Mexico. In 2020, they needed to standardize their merchandise delivery procedure and homogenize their operations so as not to rely on one or more people for the replacement of personnel. Faced with this situation, they implemented the Routal solution.
Thanks to the Planner intelligent route planner, they were able to unify processes into one, in addition to generating a single procedure that would be available to any worker regardless of their level of training.
Prior to the integration, the delivery routes were carried out manually, they spent hours daily in the planning process, there was little monitoring of the operation, and obtaining any report on performance metrics was an investment of tens of hours, which greatly limited the ability to make improvement decisions.
Once the integration of their SAP system with Routal was implemented, route planning began to be carried out in an automated manner and in minutes. The risk on the figure of the route planner and the dependence on that person was completely reduced. The creation of metric reports was also automated to improve the control and monitoring of their distribution processes, and most importantly: the data were reconciled and validated. Thus, the entire process was standardized and optimized.
”Routal Planner is essential to us. It saves us planning time and makes us more competitive against our competitors” Your Manager has your opinion.
Lácteas del Jarama Success Story: Integrating AS 400
Lácteas del Jarama It is one of the most important dairy companies in Spain, it was the first company to introduce mozzarella in our country and its history supports it as one of the main dairy companies in the food service sector.
The successful implementation of Routal was due to the successful integration of its ERP system, an IBM AS400, an extremely robust but difficult to integrate system. To be able to count on a partner like Nakima helped to be able to carry out the integration in just 3 weeks of work and thus reduce the start-up time to just over a month.
The internal leadership clearly identified the need to eliminate steps in the process that would focus logistics personnel on what really provides value: “Deliver quickly, with the lowest cost and offering the best possible service”.
The experience of working with professionals who are experts in this type of project means that companies can think further and want to improve other processes that seemed impossible to improve.
At Routal, we work to streamline integration processes through partners with a lot of experience in all types of technologies and businesses, achieving success so that projects are successful.
Try Routal for free for 10 days click here.
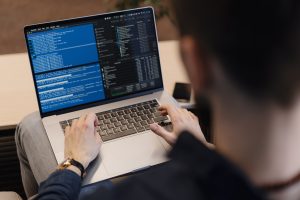