Routal blog
Why are more and more delivery people using Routal for Drivers to optimize their working hours?
Imagine this: you get home sooner, you save fuel, you know exactly what time you'll finish and, by the way, you help the planet. It's not science fiction, it's what many delivery people are already achieving thanks to Routal for Drivers, our app designed specifically for those who are behind the wheel every day.
Unlike other tools that rely on planning from a desktop, Routal for Drivers puts all the power of optimization directly in the hands of the delivery person. Literally.
Fast planning, in the palm of your hand
Forget about Excel, last-minute calls or those eternal routes that seem to have no end. With Routal for Drivers, you can upload your stops directly from your mobile phone and optimize them in seconds. It's as easy as selecting your drop off points, pressing a button and starting to drive.
The result: routes up to 30% more efficient. And that shows.
1. Time savings: get home early
Yes, we know. After many hours behind the wheel, all you want is to get home. Intelligent route optimization does just that: reduces driving time, eliminates unnecessary laps and improves the sequence of stops.
Thanks to this, many delivery people are already seeing shorter working hours while still fulfilling all their deliveries. More time for yourself, your family or just to rest.
.webp)
2. Lower fuel consumption: lower costs, more efficiency
Fewer kilometers traveled means less gasoline or diesel consumed. And that, in these times, translates into very tangible savings at the end of the month.
By avoiding unnecessary detours or poorly planned routes, Routal for Drivers helps significantly reduce fuel costs. More efficiency, more money in your pocket.
3. Better forecasts: you know exactly what time you'll finish
The app not only gives you the optimal route, but it also tells you the estimated completion time. Do you have an appointment in the afternoon or do you want to better organize your day? With Routal, you can do this without surprises or unforeseen delays.
La total visibility over your day gives you the control and peace of mind you need to plan better.
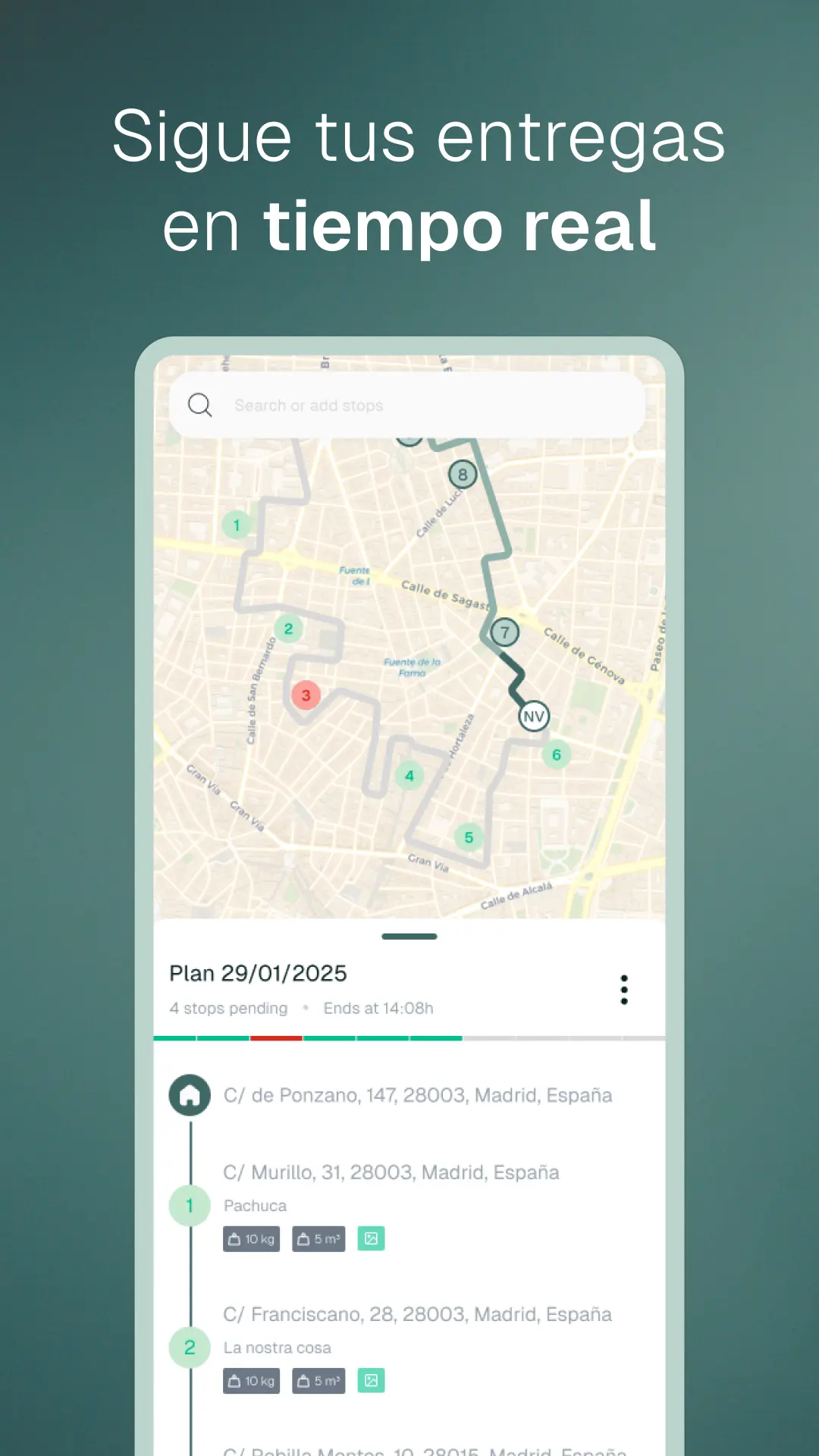
4. Lower emissions: better driving also means taking care of the planet
This benefit is enormous and sometimes goes unnoticed. By reducing the distance traveled and driving time, CO2 emissions are also reduced. That means, without changing vehicles or making costly investments, you're doing your part for a cleaner planet.
With each optimized delivery, you're contributing to more sustainable logistics.
Who is Routal for Drivers for?
For autonomous delivery people, small fleets, last-mile teams and any driver who wants to optimize their daily lives without complications. You don't need to be a logistics expert or have access to a computer: everything you need is on your mobile.
Conclusion: Drive Better, Live Better
Life on the road is intense, and any improvement counts. Routal for Drivers allows you to take control of your day, be more efficient and, above all, Get home early. Save time, fuel and stress, while doing your job more sustainably.
Haven't you tried it yet? It's time to start.
.webp)
%20(3).webp)
Has it happened to you that you end your day exhausted... but with the feeling that something is not adding up?
Spoiler: You're probably wasting more time than you think.
And that, in return, is the same as losing money.
Every day on the street is a race against the clock.
But many delivery people make invisible mistakes that sabotage their efficiency.
Here are the 3 most common ones 👇
✅ 1. Plan the route “from memory”
Trusting intuition or habit seems practical.
But all it takes is a change of traffic, a blocked road or a new badly located stop... and the chaos is served.
💡 advice: Use an app like Routal Drivers that recalculates and optimizes each route in real time.
✅ 2. Do not record incidents at the moment
Writing later, relying on memory or leaving it “for later” only brings problems.
Information is lost, forgotten, or not communicated to the team.
💡 advice: Report incidents from your mobile phone, at the same time. You win and your coordinator wins.
✅ 3. Ignore downtime between stops
It seems that nothing is going on... but those minutes add up.
Unnecessary waits, poorly ordered stops or deliveries with incomplete information. Time goes by, without you realizing it.
💡 advice: Analyze your day with tools like Routal to know exactly where your time is running out.
👉 Correct your day with Routal Drivers
Plan better.
Avoid common mistakes.
And it saves time for what really matters.
.webp)
.webp)
Have any of these mistakes happened to you?
Tell us how you deal with them 💬
%20(2).webp)
Modern logistics is no longer based solely on prior planning. Each delivery is exposed to unpredictable factors: traffic, last-minute changes, weather conditions or unforeseen events with the customer. In this context, the artificial intelligence (AI) has become a key element in anticipating problems and making faster and more accurate decisions.
Using predictive models, machine learning and real-time data analysis, companies can Anticipate delays before they occur, dynamically optimize routes and adjust your operations on the fly. This ability to react directly transforms operational efficiency, reducing costs and improving the customer experience.
In this article, we explore how AI is redefining logistics, what specific applications it offers and how tools such as Routal integrate these technologies to offer a competitive advantage to delivery and distribution companies.
What does AI bring to last-mile logistics?
Artificial intelligence allows companies to move from reactive logic to a proactive approach. Instead of waiting for a problem to arise, algorithms can detect patterns that anticipate incidents. This translates into a greater capacity to prevent delays, redistribute resources and maintain control of the entire logistics operation.
Among their most valuable contributions are:
- Delay prediction based on historical and variable data in real time.
- Identifying optimal alternative routes, depending on traffic, weather or urban restrictions.
- Automatic replanning when deviations are detected in the expected times.
- Intelligent delivery prioritization, adapted to the type of customer or level of urgency.
How does predicting delays with AI work
AI is nourished by a large amount of data: historical routes, service times, past incidents, traffic data, weather conditions, etc. Based on these inputs, machine learning models generate predictions that allow anticipate when and where delays could occur.
For example, if a delivery has been delayed four previous times in the same time zone and geographical area, the AI identifies it as a risk point and can adjust the route before it happens again.
On platforms such as Routal Planner, this functionality translates into automatic alerts for planners, to quickly identify delays and to be able to make quick and proactive decisions in the face of unforeseen events.
Use Cases: Agile Decisions in Complex Environments
1. Real-time route replanning
When a delivery person is delayed or blocked due to an incident, AI can automatically replan routes, avoiding bottlenecks and improving compliance with schedules.
2. Prioritization of critical deliveries
Based on customer behavior patterns, AI can identify which deliveries are most sensitive to delay (for example, a supermarket with high turnover or a VIP customer), and Adjust the order of distribution to ensure their punctuality.
3. Optimizing resources
In addition to improving routes, AI also helps to plan the exact number of vehicles and drivers needed, reducing excessive use of resources and adjusting shifts to real demand.
Competitive advantages of applying AI in logistics
Companies that integrate AI into their logistics operations obtain clear benefits:
- Greater reliability in deliveries, even under unforeseen conditions.
- Reduction of operating costs, by avoiding inefficient routes and intelligently reorganizing resources.
- Decrease in operational stress, since planners don't have to manually resolve each issue.
- Improving customer satisfaction, by providing more accurate information and fulfilling delivery promises.
In addition, having AI-based technology is key to scaling the operation without the need to multiply the human team.
Routal: AI integrated into every logistics decision
Routal has developed a planning system that combines predictive algorithms, data analysis and real-time monitoring. This allows companies to react before problems turn into logistical failures.
Thanks to its artificial intelligence engine, Routal offers:
- Automatic alerts for deliveries with a risk of delay.
- Instant reassignment of orders to avoid non-fulfilment.
- Alternative route suggestions that take into account traffic, restricted areas or weather conditions.
- Control panels that show operational status and possible incidents in real time.
All of this allows teams to make faster, more informed and accurate decisions.
From manual control to intelligent logistics
Modern logistics requires agility, precision and adaptability. With the help of artificial intelligence, companies no longer need to wait for a problem to appear before taking action: they can anticipate, adapt and continuously improve.
The integration of technologies such as Routal Planner allows you to automate critical decisions, reduce uncertainty and provide a more reliable delivery experience. Betting on AI is not a fad, but a key strategy to stay competitive in a market where every minute counts.
%20(1).webp)
Designing efficient delivery routes is no longer just a matter of arriving fast. Today, companies are faced with the challenge of optimizing their operations considering multiple variables at the same time: minimize delivery times, reduce logistics costs and maintain a firm commitment to sustainability. Is it possible to achieve that balance? The answer is yes, but it requires strategy, technology and a mindset aimed at intelligent efficiency.
In this article, we explain how companies can integrate these three factors —weather, cost and sustainability— in a realistic and scalable route planning model. In addition, you'll see how tools like Routal Planner facilitate this process with automation, real-time data and advanced optimization algorithms.
The pressure to deliver faster without increasing costs or polluting more is transforming logistics. Here you'll discover how to adapt without giving up on any goal.
Why is a multi-criteria approach necessary in route planning?
Traditionally, many companies have designed their logistics routes prioritizing only the shortest possible delivery time. However, this strategy ignores other key elements that directly impact the profitability and environmental responsibility of the operation.
An approach Multicriteria allows you to take into account variables such as:
- Time of delivery, to ensure punctuality and improve the customer experience.
- Operating costs, including fuel, working hours and vehicle wear and tear.
- Sustainability, with routes that minimize emissions and reduce the number of kilometers traveled unnecessarily.
Balancing these factors isn't easy manually. This is where technology comes in as a key ally.
Technology applied to intelligent planning
A solution such as Routal enables automatically design routes based on multiple simultaneous objectives. The system analyzes variables such as:
- Delivery time windows requested by the customer.
- Traffic restrictions or real-time conditions.
- Location and capacity of each vehicle.
- Geographical distribution of deliveries.
The result is a plan that prioritize efficiency without sacrificing sustainability. Thanks to optimization algorithms, each route is evaluated for its total impact, not just speed.
Practical strategies for balancing time, cost and sustainability
1. Intelligent grouping of deliveries
Grouping deliveries close geographically allows you to reduce kilometers traveled, minimize stops and improve energy efficiency. It's a simple but very powerful tactic when combined with automatic planning systems.
2. Use of Key Indicators (KPIs) for each objective
Balance can only be maintained if it is measured continuously. Some key metrics include:
- Average delivery time.
- Cost per kilometer.
- CO₂ emissions per completed route.
Routal allows you to monitor these KPIs in real time to adjust the strategy when necessary.
3. Inclusion of environmental variables
Many cities already impose restrictions on polluting vehicles. Designing routes that avoid restricted areas or that prioritize less polluting vehicles allows not only to comply with regulations, but position the brand as socially responsible.
4. Dynamic replanning for unforeseen events
Traffic, delays or customer absences are inevitable. A system like Routal can reoptimize routes on the fly, avoiding bottlenecks and ensuring that the rest of the operation is not affected.
Concrete benefits of multi-criteria planning
Companies that have adopted this model report benefits such as:
- 15-25% reduction in operating costs, thanks to shorter and more efficient routes.
- Reduction of emissions by up to 30%, combining better planning and sustainable vehicles.
- Improved NPS (Net Promoter Score) for more timely and accurate deliveries.
In addition, greater satisfaction is achieved from logistics teams, who work with less pressure and better information.
Result: Efficiency with purpose
Designing multi-criteria delivery routes is no longer an option, but a necessity for any company that wants be competitive, profitable and responsible. Balancing time, cost and sustainability is possible thanks to specialized tools such as Routal Planner, which integrate data, automation and the ability to react in real time.
Adopting this model not only improves the logistics operation. Also strengthens brand reputation, generates medium-term savings and prepares the company to respond to the new demands of the market and the planet.
.webp)
What if I told you that your route planning with Excel could be holding back your growth?
Yes, we know it works.
But we also know that it leaves a lot of room for error ❗
Do these cases ring a bell to you?
• Miscopied cells that alter the entire cast
• Drivers calling because they don't understand the order of deliveries
• Customers upset by avoidable delays
All of this is more common than it seems.
And it's not because there's a lack of effort, but because Excel wasn't designed for logistics management.
💡 When we use generic tools for critical processes, we pay for it in time, money... and headaches.
On the other hand, a specialized route software how Routal automates what you now do manually:
✓ Generate optimized routes in seconds
✓ It is updated in real time in the event of unforeseen events
✓ Share routes with your drivers and customers in one click
The result?
📉 Fewer errors
📈 More deliveries in less time
😊 And a much quieter team
The best part: you don't need to be a logistics expert or hire an engineer.
Routal adapts to your operation and scales with you.
And hundreds of companies like yours are already using it to leave logistics management behind with Excel.
👉 Find out how other companies like yours are automating it.
Does it happen to you too? Do you still rely on Excel for planning?
%20(10).webp)
Have you ever stopped to think how many euros are missing? Every day for not planning your routes well?
We're not just talking about gas or wasted time.
We're talking about deliveries you could have made, about hours you could have saved... and, yes, about Profits you could be generating if your trips were more efficient.
💡 A clear fact: a delivery man who organizes his routes well can increase his profits up to 25% only by optimizing routes and better managing your time.
Let me tell you a real case:
A last-mile self-employed man who delivered between 30 and 40 orders a day with his van started using Routal Drivers to plan your routes. Before, he made his stops “by eye” or using Google Maps. Every day I was wasting time between poorly ordered deliveries, unpredictable traffic and repeated routes.
With the app, he started to:
✓ View all your delivery points
✓ Order them automatically according to distance and times
✓ Avoid traffic jams in real time
✓ Calculate exact arrival times
The result: in a week it was already 6 more deliveries per day. And that, in real numbers, were almost 250€ more per month. Without working more hours. Only with efficient routes.
🔥 What if you too are losing money... without knowing it?
Many delivery people don't know this, but a poorly organized route doesn't just cost them gas. It costs them time, reputation and opportunities of billing.
The good news: you don't have to be a logistics expert to improve.
You only need one planning app designed for your daily life.
📲 Download Routal Drivers and try it for free.
And start earning more... without giving out more.
.webp)
.webp)
👉 Are you already using an app for your routes? Have you noticed the difference?
%20(9).webp)
Every extra kilometer, every poorly planned stop, every minute of waiting... adds up.
And the worst: a lot of times you don't even know it.
Because the hidden costs in delivery they don't appear in your reports.
👉 But they are there.
And they're draining your logistics budget every day.
The “operating normality” trap
When we talk to logistics managers, many tell us the same thing:
“That's how we've always done it.”
The problem is that Habit is not synonymous with efficiency.
Repeating planning errors or poorly optimized routes can be costing you thousands a month without you realizing it clearly.
Does it ring a bell to you?
• Routes assigned “by eye”
• Deliverances that take longer than expected
• Drivers who change routes because they “know a better one”
• Customers who call asking where their order is
Where is the money you lose hidden?
Los invisible costs appear in the form of:
✓ Gasoline wasted on poorly designed routes
✓ Overtime that is paid but not billed
✓ Deliverymen frustrated by lack of planning
✓ Customers dissatisfied with after-hours deliveries
And the worst: without accurate data, you can't correct it.
Optimize. Save. Scale.
With Routal you can detect and eliminate these leaks with surgical precision.
🚀 This is how we help our customers achieve a true logistic savings:
✔️ We optimize routes in seconds, considering traffic, time windows and vehicle capacities.
✔️ We generate automatic reports that show the hidden costs of your delivery.
✔️ We give you total control of your fleet's performance, without the need for eternal spreadsheets.
Are you missing out on these savings?
💡 Request a demo and check the savings you can achieve.
Your operation has more margin than you can imagine.
You just need to see it clearly.
%20(8).webp)
Food distribution in Colombia presents unique challenges for logistics and transportation companies. From geographical diversity to address complexity, ensuring efficient and on-time deliveries is no easy task. One of the most critical — and often underestimated — factors is the quality of the data, especially with regard to directions and geographical coordinates.
In this article, we explore how data impacts the efficiency of food logistics in Colombia and why accurate information is essential to operate successfully.
Food distribution in Colombia and Latin America: a challenging context
Colombia is a country with densely populated urban areas and vast rural regions with limited infrastructure. This territorial diversity represents a major logistical challenge for companies that distribute perishable products. Every delivery must be made in a timely manner to preserve the cold chain and ensure customer satisfaction.
Problem 1: Unstructured or unclear directions
One of the main obstacles is the inconsistency in writing addresses. In many regions, addresses do not follow a standard format and may include non-technical references such as “in front of the school” or “next to the big tree”.
This type of information may work for a local delivery person, but not for an automated route planning system. The lack of structure makes geocoding difficult and slows down the entire logistics process.
Problem 2: Absence of accurate GPS coordinates
Geographic coordinates are the most reliable way to identify exact locations. When companies don't have precise coordinates associated with their addresses, optimization algorithms lose efficiency.
This can translate into:
- Longer or poorly calculated routes
- Increases in fuel consumption
- Delays in deliveries
- Difficulties calculating realistic time windows
Have access to reliable latitudes and longitudes significantly improves system performance and reduces the margin of error.
Solution: How Routal improves food logistics in Colombia and Latin America
Routal is a SaaS solution designed to plan, optimize and monitor distribution routes. To achieve this precisely, it relies on high-quality data and advanced geolocation tools.
Among its key features:
- Automatic address normalization: Convert ambiguous descriptions into standardized formats.
- Precise geocoding: Transforms addresses into ready-to-use coordinates.
- Integration with updated maps and local geographic databases.
- Planning based on real data: allows you to calculate routes considering logistics restrictions, delivery times and business priorities.
Summary: Data is the basis for efficient logistics
Last-mile logistics in Colombia, especially in the food sector, requires more than vehicles and routes: it needs clean, structured and georeferenced data.
Investing in information quality is key to reducing costs, increasing efficiency and improving the end customer experience.
With tools like Routal, companies can transform operational chaos into a fluid, automated and reliable system.
%20(7).webp)
The last mile is one of the most critical and complex sections of the entire logistics chain. And although we often talk about route optimization or cost reduction, there is an equally crucial aspect that is often overlooked: communication between the key actors in the cast. We refer to logistics managers, delivery people and, of course, end customers.
In this article we are going to break down the main communication problems that currently exist, why they continue to occur and, most importantly, how we can solve them using modern tools and more efficient flows.
📞 The phone: the king who no longer reigns
In many delivery companies, the main communication tool is still the telephone. It's a fast, straightforward, and widely adopted solution. But it is also the source of numerous problems that directly affect operational efficiency.
Problems with (synchronous) telephone communication between manager and delivery person
- Time lock
- A call requires simultaneous attention from both people. If you are busy, the entire operation is delayed.
- Constant interruptions
- The manager interrupts the delivery person to answer questions or make adjustments, affecting their concentration and productivity.
- Mutual dependence
- If the delivery person doesn't answer, the manager is left without information. If the manager is not available, the delivery person gets frustrated.
- Lack of traceability
- The calls leave no clear or organized record of what has been said or agreed.
- Coverage or noise issues
- In rural areas or noisy environments, voice communication is inefficient or even impossible.
🧍 ♂️📱 Deliver-customer communication: the big bottleneck
The other major battle front in the last mile is the interaction with the end customer. Here, too, the telephone reigns, with equally questionable results.
Main customer communication issues
- Last-minute alerts
- Many delivery people call just a couple of minutes before arriving, leaving little room for the customer to react.
- Unanswered calls
- The customer may be busy, at work, or without coverage. This requires repeated attempts, causing delays.
- Unnecessary waste of time
- Coordinating deliveries over the phone multiplies downtime, especially when you have to retry or wait for answers.
- Ambiguity and errors
- Poorly indicated addresses, unclear instructions, or last-minute changes without documentation.
- Unnecessary tension
- Calls can lead to misunderstandings or even conflicts if there are unpunctualities or unmet expectations.
💡 How to improve communication in the last mile?
1. Using Asynchronous Messaging Platforms
Tools such as Routal they make it possible to establish asynchronous communication channels where information flows without the need for both parties to be available at the same time. This allows:
- Leave clear, written instructions.
- Record incidents and inquiries.
- Send automatic notifications about the status of the cast.
- Notify in advance, generating options for the end customer and for the manager.
2. Smart notifications for the customer
Customers can receive automatic notifications by SMS, email or WhatsApp stating:
- Estimated time of arrival.
- Number of stops remaining before yours.
- Possibility to change the time or place of delivery from the mobile phone.
- Ability to send messages to the delivery person to find solutions or alternatives
3. Real-time tracking portals
A solution such as Routal allows us to offer the customer a tracking link where you can see the location of the delivery person and their progress. This reduces unnecessary calls and increases customer satisfaction.
4. Quick feedback and issue forms
Both the delivery person and the customer can report problems in a structured way (damaged package, wrong address, missing customer...), which avoids long calls and centralizes management.
5. Integration with planning and CRM tools
By having all the information centralized, the logistics manager can make faster and more data-based decisions: redistribute routes, assign tasks, anticipate delays or manage incidents.
🧭 Result
The last mile is not only about kilometers traveled, but about people who understand each other (or not). If we continue to rely on the telephone as the only communication tool, we are doomed to a system that is fragile, inefficient and difficult to scale.
Moving to smarter solutions such as Routal improves coordination, reduces errors and, above all, Save time for the whole team. Because in the end, good communication doesn't just deliver packages... Give peace of mind.
If you feel that you have this type of problem, I encourage you to try Routal Planner or Schedule a call.
%20(6).webp)
Until now, enjoying advanced technology to plan routes, save gas or replan deliveries in real time seemed like a luxury reserved for large companies. But that's over. With the new application Routal Drivers, autonomous drivers can now access the same tools that large fleets use... from their mobile and in a matter of minutes!
What makes Routal Drivers so special?
We know what it means to be self-employed: every minute counts, every liter of gasoline adds up, and every diversion can mean a failed delivery. That's why Routal Drivers has been designed with you in mind, the driver who does everything. Here are some of its main advantages:
⏱️ Time savings
Routal Drivers automatically generates the best possible route for all your stops of the day. Forget about wasting time reorganizing maps or looking for directions. The app does the work for you, optimizing each journey.
⛽ Fuel savings
Thanks to smarter and more efficient routes, you'll spend less on fuel. That translates directly into more benefits for you, without changing the way you work.
📍 Reach customers faster
Do you have deliveries in new or complex areas? Routal Drivers precisely guides you to the customer's door, using real-time information about traffic and road conditions.
🔄 Replan as you go
Do you have a new stop while you are en route? Does the customer change your address? With Routal Drivers you can add, remove or reorder stops at any time, and the application recalculates your route instantly.
🚶🚴🚛 Multi-mode of transport
It doesn't matter if you go by van, bike or on foot: Routal Drivers adapts to the way you move, to offer you the best route depending on your vehicle and the type of delivery you make.
📲 Download it now and start saving
Whether you're a freelance deliveryman or you're working as a freelancer for marketplaces or small businesses, Solo Drivers is made for you.
Routal now puts technology in your hands. You don't need to be a big company to work like one. Grow your business with Solo Drivers!