What is fulfillment? The answer to your logistics questions
.jpg)
If you have a business that sells physical products, you've probably come across the term Fulfillment. But what exactly does it mean? How can fulfillment help improve your company's logistics? In this article, we help you answer all your questions about the Fulfillment and its importance in the supply chain.
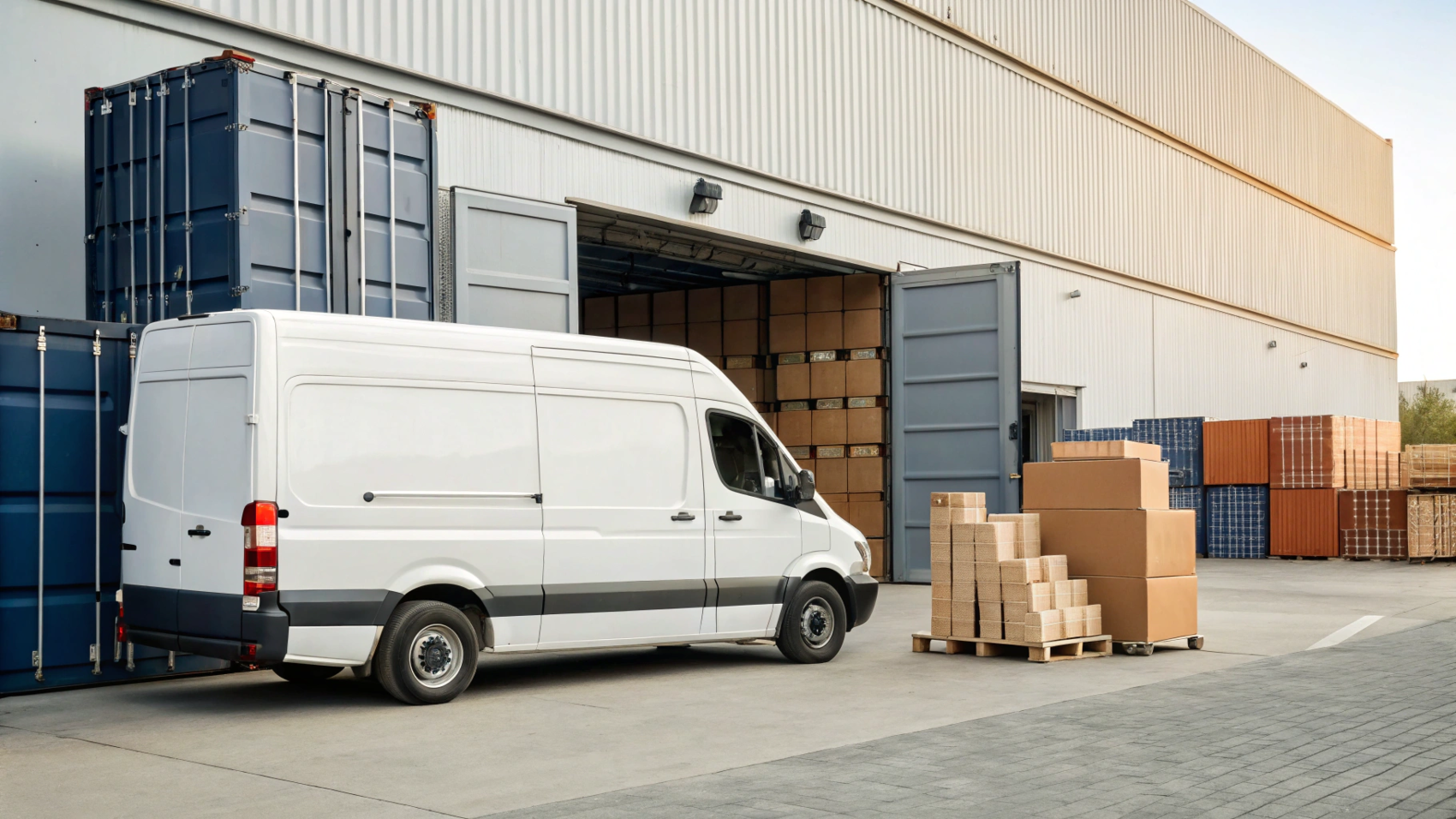
What is fulfillment?
The term Fulfillment refers to the complete process that a company carries out from receiving an order until the product reaches the customer. It's not just about shipping the package, but a series of steps that ensure that the purchase is made efficiently and that the customer has a satisfactory experience.
In other words, the Fulfillment encompasses all logistics operations that make it possible for a customer to receive their order correctly and in the shortest possible time. This process includes:
- Receiving and storing inventory.
- Order Management.
- Picking (selection of products in the warehouse) and packing (packaging).
- Shipping and distribution.
- Follow-up and customer support.
- Returns and post-sales management.
El Fulfillment it's not just a logistical issue, but it has an impact directly on the reputation and success of a business. The speed, accuracy and reliability of the process can make the difference between a satisfied customer and one who will never buy again.
According to some surveys, 83% of customers would never buy from an online store again if they had a bad delivery experience. The most common problems include shipping delays, incorrect products, damaged packages, or lack of tracking information.
For this reason, companies are increasingly investing in technological solutions and automation to optimize the Fulfillment, reduce operating costs and improve customer satisfaction.
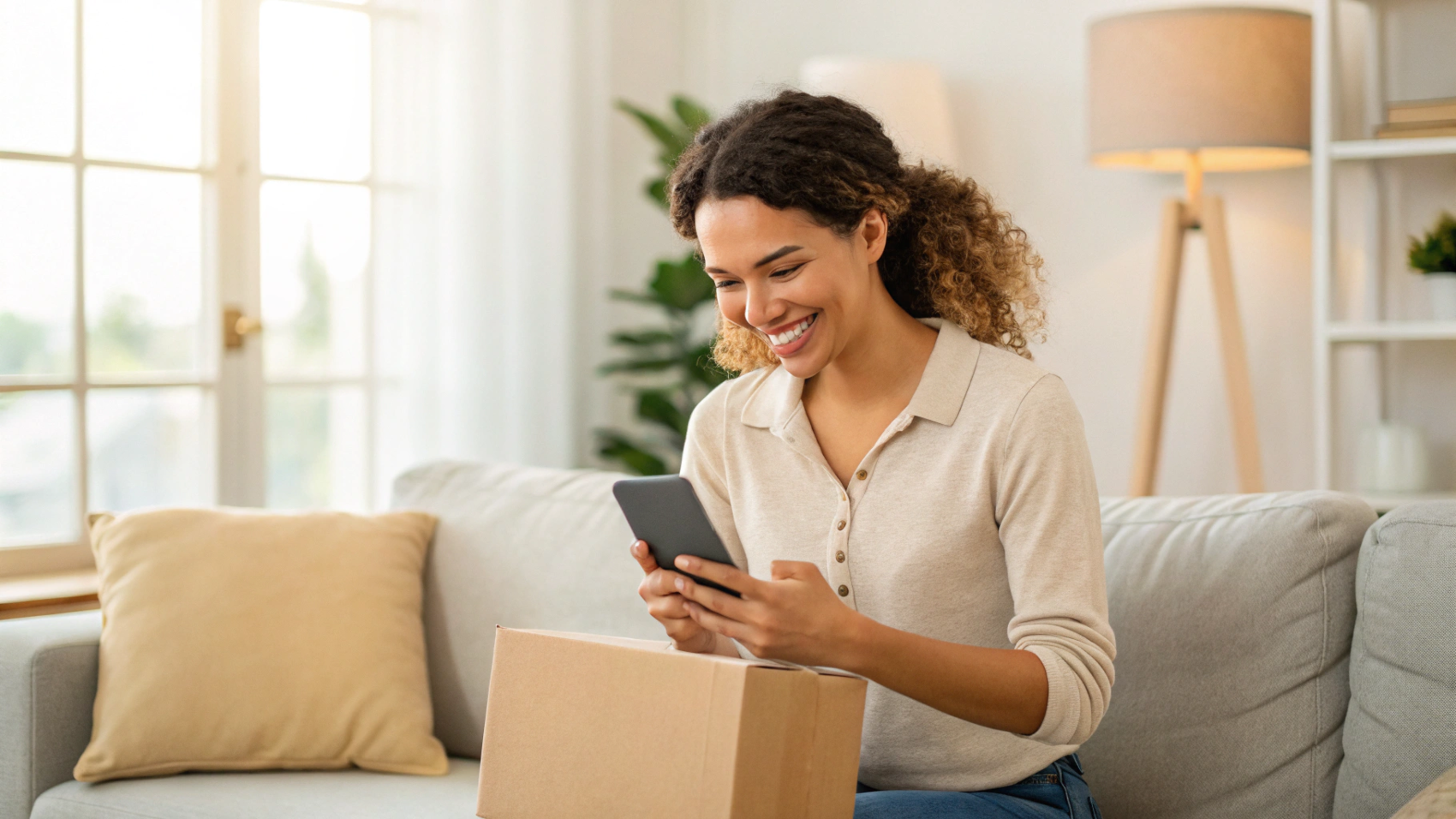
Types of Fulfillment:
• Fulfillment internal: The company manages the entire warehousing, order preparation and shipping process from its own facilities. It's a strategy that allows for greater control over inventory and customer experience, but it also requires significant investment in infrastructure, people and technology.
• Fulfillment outsourced (3PL): An external company specialized in logistics manages the storage, preparation and shipment of orders. This option allows companies to reduce operating costs and scale more easily, since 3PL providers have advanced infrastructure and technology to handle large volumes of orders. However, by depending on a third party, a certain level of control over delivery times and the personalization of the service is lost.
• Fulfillment by marketplace: In this model, the marketplace is responsible for the storage, packaging, and shipping of products on behalf of the seller. This is an increasingly popular alternative, especially for businesses that sell through platforms such as Amazon, Walmart or eBay. A clear example is Fulfillment by Amazon (FBA), where products are stored in Amazon distribution centers and are shipped directly to the customer with the platform's service standards. This option simplifies logistics and allows for quick deliveries, but it also involves high costs and a lower capacity for differentiation, since the packaging and delivery experience are controlled by the marketplace.
• Fulfillment hybrid: Combines different strategies of Fulfillment, for example, managing some products internally and delegating others to 3PL or marketplaces. This combination makes it possible to optimize costs and better manage demand in peak seasons without compromising the company's operational capacity. However, it requires efficient coordination and advanced technological tools to synchronize different workflows.
Why is it important to have a good fulfillment system?
- Reduction of delivery times.
- Reduction of errors in shipments.
- Optimization of logistics costs.
- Increased customer satisfaction.
- Ability to handle large volumes of orders.
How to have a good fulfillment system with technology?
If you manage a model of Fulfillment internal, where the entire process of storing, preparing and shipping orders takes place within your company, it is essential to have technological tools that optimize the operation. Without the right technology, this model can become costly, inefficient, and difficult to scale.
Route optimization tools such as Routal, allows the last mile to be more efficient, ensuring that orders arrive in a timely manner. By integrating route planning software with your Fulfillment, you can reduce costs, improve delivery visibility and increase customer satisfaction.
In addition, in Routal We recently visited the Amazon DCT9 in Barcelona, one of its main logistics centers, to understand first-hand the processes and challenges of last-mile distribution in one of the largest companies in the world. This experience has allowed us to strengthen our technological solutions, aligning them with the best practices in the sector to offer our customers high-level logistics management.
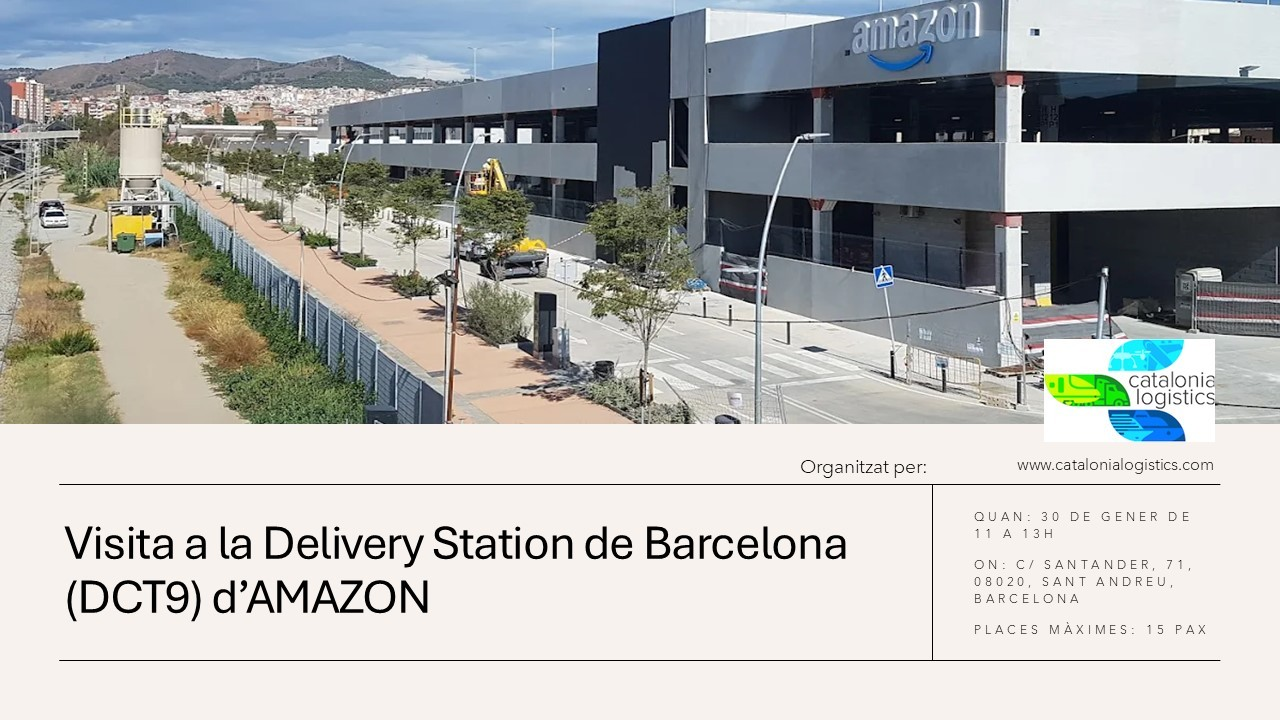
.jpg)