The 7 tips you need to improve the reverse logistics process
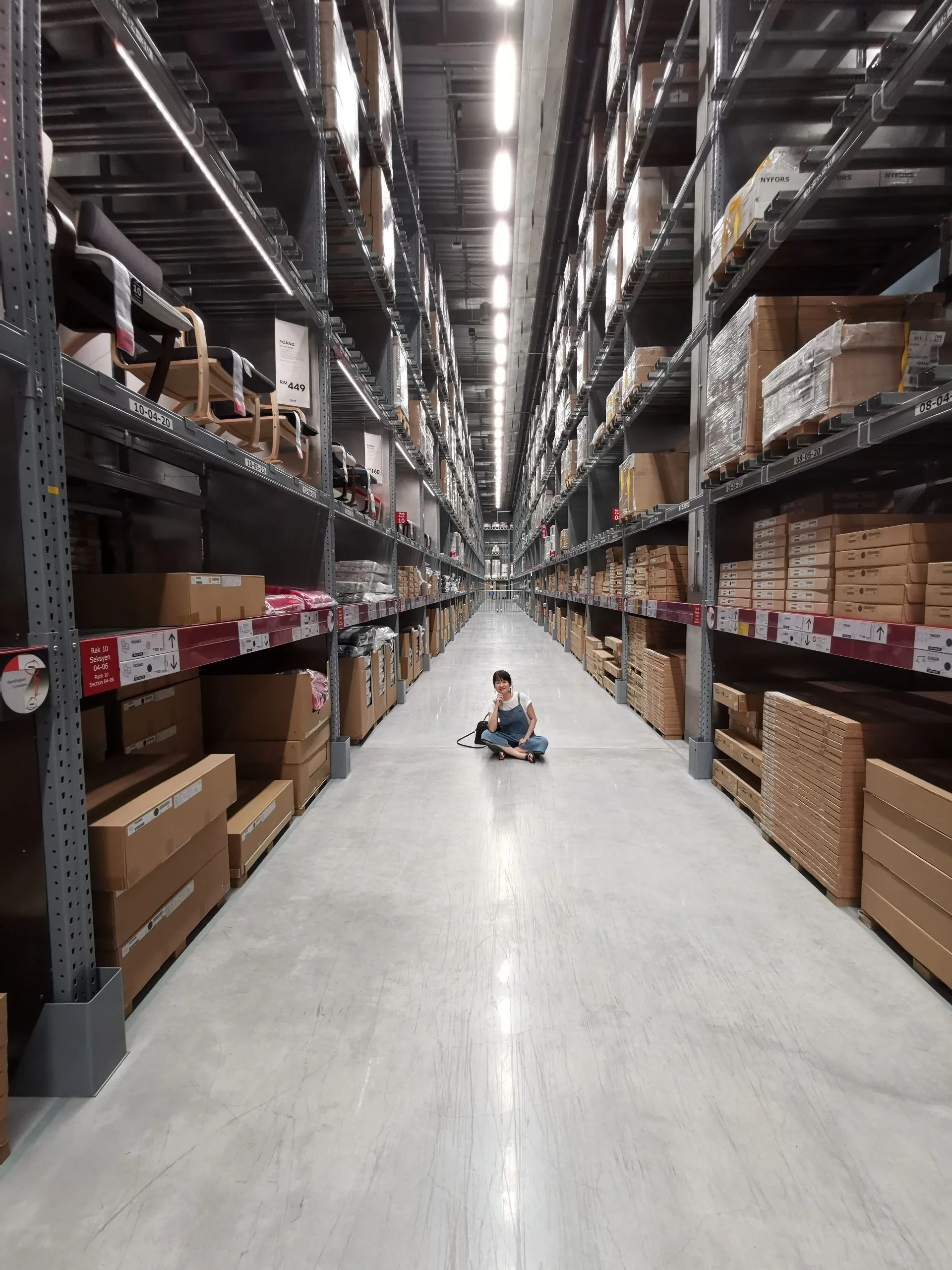
The logistics industry is constantly changing, both in processes and in the way of proceeding. These changes are due, to a large extent, to technological advances in the sector, which evoke different modalities in logistics processes, such as reverse logistics.
What is Reverse Logistics?
Reverse logistics is the set of practices and processes responsible for managing the returns and returns of those products purchased by users.
These returns or returns are managed from the points of sale of the products to the manufacturer itself (to carry out the repair, recycling or disposal of the product at the lowest possible cost).
In addition, reverse logistics is already another process and of vital importance when planning the supply chain for the satisfaction of the end customer.
7 tips to improve your reverse logistics
Customer Centric: It responds to the customer-oriented strategy through which an organization places the customer at the center of the company with the objective of focusing all processes and operations on users.
The implementation of the Customer Centric strategy increases the satisfaction of our users, since we focus all our efforts on knowing their needs and concerns regarding our activity. Knowing the desired delivery and return times or a maximum price per service will help increase your satisfaction and, therefore, carry out a satisfactory reverse logistics process.
Strategic Planning: Perform measured and analytical planning to ensure the correct management of operations taking into account parameters such as mileage or travel time. With the right software, this will be an autonomous task, in which a large amount of time is not required and with an optimal result, since it will always offer the most efficient route.
Optimization of resources: The optimization of resources when it comes to transportation is essential for the success of your company's reverse logistics process; it will help control the traceability, trajectory and tracking of shipments. In addition, planning delivery routes efficiently and optimally will result in significant economic and time savings. Therefore, the use of specialized software for route planning will be a key element in increasing the efficiency of your company's reverse logistics process.
Use of metrics and KPIs: To evaluate the productivity and performance of the reverse logistics process, the use of KPIs is essential (Key Performance Indicator). These indicators will help measure and quantify your company's performance and compliance with established objectives. It is recommended that when defining the logistics KPIs, they are developed based on the S.M.A.R.T. (Smart, Mmeasurable, Achivable, Realistic and Time-Bound) model.
Shorter return times: As mentioned before in relation to the Customer Centric strategy, it is essential to know not only the limits of our company in terms of acceptable delivery or return times, but also the “deadlines” or desired deadlines of our customers. For this reason, and in general terms, it should be prioritized that collection and return times are as short as possible and without the need to increase the amount of resources associated with reverse logistics. Thus, specific efforts should be made to improve this particular process.
Proactive monitoring: Proactive monitoring is the live monitoring of the daily planning of services and deliveries that warns of possible failures and errors while allowing us to react and adapt operations in a satisfactory manner.
Good proactive monitoring must have the possibility of monitoring the operation in real time and thus be able to view the progress of the operation live at all times. In addition, and in relation to the real-time monitoring of operations, it is essential that it incorporates sufficient functions that allow a timely reaction to possible failures or errors.
Non-intelligent warehouses or Smart Storage: Smart warehouses are specialized logistics centers that make use of technology to increase efficiency in all their processes, such as the reception, preparation or storage of goods.
An example of the use and benefit of implementing intelligent warehouses in the reverse logistics process is the case of Amazon, a company that has included artificial intelligence in its warehouses in order to quickly determine, based on the costs of each product and its associated return costs, if it accepts to pick up the product in question by activating the reverse logistics process or, on the contrary, makes the refund without the collection of said merchandise.
If you want to guarantee the success of your company's reverse logistics process, you can do so now with the specialized SmartMonkey Planner software. Try it free for 10 days, for a limited time only.